Ventilation and Air-Conditioning Systems
Ventilation and air-conditioning systems (VAC systems) are the heart-lung machines of pharmaceutical clean rooms. VAC systems are used to condition the air, to generate the required air cleanliness and to distribute the air. There are numerous requirements for the design, construction and operation of VAC systems as well as for the required air cleanliness. Compliance is demonstrated by means of qualification and controlled by carrying out GMP inspections. The requirements such as the number of particles in the air, the rates of air circulation, the recovery times, the flow direction etc. are controlled in the clean room. In the GMP environment the clean room is also controlled microbiologically by means of contact samples and air pathogen samplers. The terminal HEPA filter in the supply air in the ceiling of the clean room is the interface between VAC systems and clean room. On account of the system the HEPA filter is not a 100% tight, however, and although these filters ought to be controlled regularly as concerns their integrity, undiscovered damages or leakages may adversely affect the clean room`s quality. Usually, uncontaminated extract air is extracted without a filter at the clean room`s ceiling, and is only cleaned by means of a central filter in the VAC unit before being discharged into the environment as exhaust air. This means that it is not possible to exclude re-contaminations completely. The ventilation technology may not be a source of contamination itself and is supposed to guarantee breathing air conducive to good health. This calls for operator responsibility as concerns personal protection. Moreover, a hygiene-compliant VAC system also ensures that the ventilation won`t pose a microbiological risk for the products manufactured in the clean room. This means that the VAC system ensures product protection. This is where the guideline series VDI 6022 "Ventilation and indoor-air quality" concentrates on. Both points are achieved by a hygiene-compliant design as well as by a hygiene-compliant maintenance including a hygiene inspection of the system - described in the VDI 6022 series [Part 1].
Compliance with the requirements concerning hygiene can be controlled and documented by means of a hygiene inspection according to VDI 6022. This inspection is also an essential element of the hygiene-compliant operation of ventilation and air-conditioning.
Ventilation, Hygiene and Hygiene Maintenance
Ventilation and air-conditioning systems (VAC systems) are the heart-lung machines of pharmaceutical clean rooms. VAC systems are used to condition the air, to generate the required air cleanliness and to distribute the air. There exist numerous requirements for the design, construction and operation of VAC systems as well as for the required air cleanliness. Compliance is demonstrated by means of qualification and controlled by carrying out GMP inspections. The requirements such as the number of particles in the air, the rates of air circulation, the recovery times, the flow direction etc. are controlled in the clean room. In the GMP environment the clean room is also controlled microbiologically by means of contact samples and air pathogen samplers. The terminal HEPA filter in the supply air in the ceiling of the clean room is the interface between VAC systems and clean room. On account of the system the HEPA filter is not a 100% tight, however, and although these filters ought to be controlled regularly as concerns their integrity, undiscovered damages or leakages may adversely affect the clean room`s quality. Usually, uncontaminated extract air is extracted without a filter at the clean room`s ceiling, and is only cleaned by means of a central filter in the VAC unit before being discharged into the environment as exhaust air. This means that it is not possible to exclude re-contaminations completely. The ventilation technology may not be a source of contamination itself and is supposed to guarantee breathing air conducive to good health. This calls for operator responsibility as concerns personal protection. Moreover, a hygiene-compliant VAC system also ensures that the ventilation won`t pose a microbiological risk for the products manufactured in the clean room. This means that the VAC system ensures product protection. This is where the guideline series VDI 6022 "Ventilation and indoor-air quality" concentrates on. Both points are achieved by a hygiene-compliant design as well as by a hygiene-compliant maintenance including a hygiene inspection of the system - described in the VDI 6022 series [Part 1].
Compliance with the requirements concerning hygiene can be controlled and documented by means of a hygiene inspection according to VDI 6022. This inspection is also an essential element of the hygiene-compliant operation of ventilation and air-conditioning systems. With regard to hygiene inspections according to VDI 6022 a distinction is made between "initial hygiene inspection" and "repeated hygiene inspections" (short: hygiene inspections).
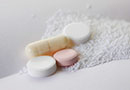
Recommendation
14-16 October 2025
Granulation & Tableting - Live Online Training
The inspection is carried out by an indoor-air quality manager, a VDI-certified specialist engineer or an expert having a Category A qualification according to VDI 6022 Part 4. The responsibility for the hygiene in VAC systems and especially for the performance and documentation of hygiene inspections lies with the owner of the VAC system or with the operator whom the owner has obligated by contract or by a written undertaking precisely for this.
It is not an explicit GMP requirement to comply with VDI 6022 or to perform hygiene inspections. According to common GMP understanding, however, it is not the terminal HEPA filter but the ventilation and air-conditioning system upstream of the HEPA filter that generates the indoor-air quality. Equally, pharmaceutical water isn`t obtained by means of filters in the distribution system but by means of the purification process in the high-purity water system. This means that in the general context the operation of a hygienic ventilation system can indeed be understood as a GMP requirement. Regarding this the VDI 6022 series shows a way to reach this goal and offers help to establish a system for the ongoing operation.
Initial Hygiene Inspection
Pursuant to the guideline the initial hygiene inspection shall be performed by qualified personnel having at least a Category A qualification according to VDI 6022 Part 4.
The initial hygiene inspection is to be carried out:
- regarding new systems after completion and before use
- after having carried out substantial changes at VAC systems and if possible before further use
- regarding existing systems in relation to which no initial hygiene inspection has been carried out so far
The initial hygiene inspection is recommended for example in the case of an operator change at the beginning of the operator`s activity.
The initial hygiene inspection includes the following in addition to the contents of the repeated hygiene inspections:
- the verification of implementation of and compliance with the requirements concerning planning, design, manufacture, execution and assembly
- specification and documentation of the minimum required locations for hygiene checks and repeated hygiene inspections
- an additional leakage test of the air duct system (report available, carry out optional measurements if appropriate)
Periodical Hygiene Inspections of VAC Systems
General
As already said, hygiene inspections are to be performed by qualified personnel having at least a Category A qualification according to VDI 6022 Part 4.
Hygiene inspections shall be performed:
- for ventilation and air-conditioning systems with humidification every two years
- for ventilation and air-conditioning systems without humidification every three years
If more than 20 decentralised units (only assigned to one room) or terminal units (without having an own drive for air conveyance) of identical type and identical mode of operation are installed in a building, the hygiene inspections are to be performed on a wellfounded, representative random selection of units. If hygiene inspections yield critical results in more than one unit, all units and terminal units have to undergo thorough cleaning and disinfection. The hygiene inspection is to be extended to include all air-handling units, at least for the turn in question.
Hygiene inspections are performed in order to detect deficiencies and initiate measures for remedying the deficiencies. Hygiene inspections include the following activities.
Extended Visual Inspection
An extended visual inspection of the VAC system as regards hygiene deficiencies (such as contamination, corrosion, limescale, damages, leakage of lubricant) is to be carried out. Visual microbial contamination identified in the course of the visual examination is a critical result.
Leak Test of the Air Distribution System
As regards air ducts and built-in components VDI 6022 Part 1 recommends a specific tightness class depending on the pursued cleanliness class of the air ducts and components.
For air ducts for general working areas in the industry VDI 6022 requires cleanliness class "middle" and tightness class C according to DIN EN 12237 / DIN EN 1507. For rooms with higher requirements as concerns the air quality such as laboratories etc. the cleanliness class "high" and the tightness class D are recommended. (Notice: The tightness classes A-D have nothing to do with the cleanliness classes A-D according to EU GMP).
Usually, the tightness class and the cleanliness class depend on the relevant building and room types that are described as application examples in VDI 6022 Part 1 table 1. Comparable to laboratories clean rooms should be classified in cleanliness class "high" and in tightness class D. The aim is to prevent the spreading of contaminations by means of air ducts or the ventilation system in the system or building. This may be the case for instance in vacuum situations or if the ventilation system stands still (for instance in the case of a power failure or fire damper closure).
These recommendations of VDI 6022 only concern the planning in the first instance. Leak testing at handing over of the property and hygiene inspections are not required explicitly in VDI 6022 but they are highly recommended for several reasons:
- definition of a reference value for the hazard assessment
- ensuring perfect operation at handing over of the system
- ensuring the hygienic functioning of the system
Moreover, due to incorrect transportation and especially because of defective installation the real tightness of a VAC system can be significantly worse than the tightness class indicated by the manufacturer of the ducts.
If a leak test is carried out on site it should include at least a visual inspection of the mounted air duct system on site. If a supplementary measurement is carried out in addition to the leak test performance according to DIN EN 12599 is recommended. The result of a leak test is a result record which indicates the cause for a leakage to the operator. The potentially found leakage problems have to be remedied by the operator or by a third company.
Microbiological Tests
General
Microbiological tests are carried out to localise sources of bacteria or mould in the VAC system. A contamination of the room air with bacteria or mould spores has to be prevented in any case.
The amount of dust, bacteria, mould or other biological substances in the supply air may not in any category exceed the amount in the reference air (outdoor air or room air).
The hygienic condition has to be checked including specific contact sampling of hygiene-relevant sampling locations. Potential locations for microbial sampling are primarily found in regions prone to microbial growth. These are for instance: air filter chambers, fan chambers, silencers, cooling tube bundles, heat recovery systems, condensate trays, droplet eleminators and humidifier chambers.
Microbiological Tests in Waters
In ventilation systems for clean rooms steam humidifiers have to be installed for humidification as a matter of principle. The requirements described below for systems with recirculating water can also be used for humidification with steam. In this case feed water of the steam system and the condensate of the steam have to be used.
- Determination of the total number of colony-forming units in the recirculating water of air humidification systems and comparison with the reference values (table 1).
- Sampling for the determination of the concentration of Legionella spec. and where applicable of pseudomonads in the recirculating water of air humidification systems. Incubation on selective media shall only be carried out in laboratories approved in accordance with Section 44 of the Law on the Protection from Infectious Diseases (IfSG). An exceedance of standard values is a critical result.
- Are recirculating water systems used there is the obligation to furnish proof of the sampling. The operating manual has to be provided as evidence for this.
- The operator is required to provide proof of the testing of the drinking water quality in supply water according to VDI/DVGW 6023 and according to the German Drinking Water Ordinance (TrinkwV).
Table 1: Microbiological methods and reference values [1]
Parameters | Humidifier water |
Total amount of colony-forming units (bacteria)1 according to ISO 6222 or TrinkwV | < 1000 CFU/ml |
Legionella spec.2 according to ISO 11731 and ISO 11731-2 | < 100 CFU/100 ml |
Pseudomonas aeruginosa3. King B Agar, 36 °C, 48 h DIN EN ISO16266 | < 100 CFU/100 ml |
1 Total number of colony-forming units: Need for action in the case of deviations from the basic state > factor 10
2 Legionella spec.< 100 CFU/100 ml okay, < 1000 CFU/100 ml monthly examination, < 10000 CFU/100 ml pulse dosing of biocide, > 10000 CFU/100 ml hazard prevention and remediation
3 Pseudomonas aerogiosa < 100 CFU/100 ml okay, < 1000 CFU/100 ml inspection and desinfection, >1000 CFU/100 ml inspection, disinfection and remediation
Microbiological Testing of Surfaces
This test can only be carried out by microbiological laboratories. One possibility to prove this is a DAkkS accreditation according to DIN EN ISO /IEC 17025. Sampling is carried out by the laboratory or by a trained person who can prove to have at least a Category A qualification according to VDI 6022 Part 4.
Procedure
- Sampling of the surfaces according to DIN 10113-3 with two contact plates, DG18 for moulds and yeasts, CASO for the total amount of colony-forming units
- Incubation of the culture media for seven days (moulds/ yeasts) at 25°C and for two to three days (total amount of CFUs) at 30 °C
- Repeated counting of the colonies during the incubation time
Care must be taken to ensure that the sampling location is cleaned thoroughly after sampling.
Analysis
The analysis is carried out separately for the total amount of CFUs and the moulds/yeasts by means of the empirical values in table 2. The results must be assessed within the context of the overall hygienic condition of the system under test.
Table 2: Empirical values and measures to be taken after surface measurements [1]
Result* in CFU/25 cm² | Assessment and measures to be taken |
< 25 | Surfaces tested are in good or very good hygienic/microbiological condition. No action required. |
25 to 100 | Hygienic/microbiological condition of the surfaces tested is on the borderline. Find cause, eliminate. Thoroughly clean elements concerned, or plan replacing them in the near future. Add to cleaning and maintenance schedule. |
> 100 | Surfaces tested are in insufficient hygienic/microbiological condition. Find cause, eliminate. These elements are in urgent need of thorough cleaning and additional disinfection, where applicable, or replacement as required. Immediate action required! |
* Total for each plate (bacteria + moulds/yeasts)
If deficiencies with regard to hygiene are detected the causes for these have to be determined and the operator has to rectify them or to outsource the rectification to an external company.
Microbiological Testing of the Air
This test which became obligatory with the revised version of VDI 6022 can only be carried out by microbiological laboratories or by companies having sufficient experience with the measurement and ventilation technology. One possibility to prove this is a DAkkS accreditation according to DIN EN ISO /IEC 17025. Sampling is carried out by the laboratory or by a trained person who can prove to have at least a Category A qualification according to VDI 6022 Part 4.
Procedure
Sampling of the air for instance with RODAC plates, DG18 for moulds and yeasts, CASO for the total amount of colony-forming units.
With regard to the techniques and media used, sampling shall conform to, e. g., DIN ISO 16 000-16 to -18.
Analysis
Given the requirement that the supply air shall not be poorer in terms of content and spectrum of pathogens (moulds, yeasts, bacteria) when compared to the respective reference air, differentiation at least of the mould species is mandatory.
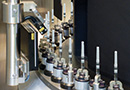
Recommendation
Vienna, Austria21-23 October 2025
Visual Inspection of Parenterals PLUS Pre-Course Fundamentals of Visual Inspection
Contamination of Surfaces
Visual Assessment of the Dust Surface Densitiy In order to determine the level of contamination of the air ducts a simple visual assessment is sufficient (see [3] VDI 6022 Part 1.3). The visual assessment is carried out by qualified personnel having at least a Category A qualification according to VDI 6022 Part 4.
Documentation of the Activities
- Sampling locations should be marked permanently and they should be accessible.
- Each hygiene inspection has to be documented and to be archived reproducibly by the operator.
- The date for a required verification of the implementation and success of the recommended measures shall be specified depending on the urgency of the measures to be taken. The same holds for the notification of completion of remedy of any hygiene deficiencies established.
- If a critical result is found further specialised personnel is to be consulted.
- Consulting the company physician is mandatory if employees or personnel working in the rooms served by the ventilation and air-conditioning system experience disturbances or physical disorders. If necessary, the system must be shut down and remedial action has to be taken at short notice.
- Hazard assessment according to VDI 6022 Part 1 Annex B
-with regard to those exposed to the air supplied by the VAC system
-for activities of the maintenance personnel
. German Safety and Health at Work Act (Arbeitsschutzgesetz, ArbSchG)
. German Ordinance on Industrial Safety and Health (Betriebssicherheitsverordnung, BetrSichV)German Workplace Ordinance (Arbeitsstättenverord nung, ArbStättV)
. German Hazardous Substances Ordinance (Gefahrstoffverordnung, GefStoffV)
. German Hazardous Substances Ordinance (Gefahrstoffverordnung, GefStoffV)
. German Biological Agents Ordinance (Biostoffverordnung, BioStoffV)
Hygienic Technical Requirements Concerning VAC Systems
The following checklist defines the most important aspects of the hygiene inspection
Number | Component | TARGET State | ACTUAL State |
1 | Outdoor-air inlets and |
| |
2 | Central air-handling |
| |
3 | Air filters |
| |
4 | Air humidifiers/ recirculating |
| |
5 | Air humidifiers/ steam |
| |
6 | Heating and cooling |
| |
7 | Heat recovery system |
| |
8 | Fans |
| |
9 | Air ducts |
| |
10 | Silencers |
| |
11 | Air outlets |
| |
12 | Underground ducts |
| |
13 | Operation and maintenance |
|
Level of contamination: G = low, M = middle, S = high, F = humid
Hygiene Inspections Carried out at VAC Systems according to VDI 6022
About the Authors
Nikolaus Ferstl
...has been the technical director of the University Hospital and the University of Regensburg since 2009. He is also a freelance consultant
for building and cleanroom technology.
Source:
[1] VDI 6022 Part 1 Ventilation and indoor-air quality – Hygiene requirements for ventilation and air-conditioning systems and units (VDI Ventilation Code of Practice), date of issue: 2018-01
[2]VDI 6022 Part 3 – Ventilation and indoor air quality – Assessment of indoor air quality, date of issue: 2011-07
[3]VDI 6022 Part 4 Ventilation and indoor-air quality – Qualification of personnel for hygiene checkings, hygiene inspections, and assessment of indoor-air quality, date of issue: 2012-08
[4]VDI 6022 Part 4.1 Ventilation and indoor-air quality – Qualification of personnel for hygiene checkings, hygiene inspections, and assessment of indoor-air quality – Certificate of competence in Category A and Category B, date of issue: 2014-03
[5]VDI 6022 Part 6 Ventilation and indoor-air quality – Air humidification by decentralised devices – Hygiene in planning, construction, operation, and maintenance, date of issue: 2018-01
[6]VDI 6022 Part 7.1 Ventilation and indoor-air quality – Branch-specific guides – Waste treatment plants, date of issue: 2013-10