Reusable wipe covers - GMP-compliant and process-safe in use
Wipe covers are used for manual cleaning and disinfection of larger room surfaces (floor, wall, wall elements, outer surfaces of equipment, ceiling, etc.). Cleaning and disinfection of these surfaces removes contaminants that can negatively affect the quality of the products manufactured in the room as well as the processes taking place there, and maintains the specified cleanliness status of GMP cleanrooms. The "cleaning" and "disinfection" measures are thus processes which impact the quality and therefore an important part of the contamination control strategy. However, the cleaning and disinfection measures can also lead to contamination risks if not carried out properly. Therefore, it is necessary that the cleaning and disinfection measures are not only systematically planned, but also implemented in a practical manner and tested for their efficiency. It must also be ensured that the individual components are coordinated as well as suitable for the respective process in the respective cleanroom, that the personnel is trained, and that all necessary documents for implementation and verification are available. If operating equipment and disposables are used several times and reprocessed for this purpose, the suitability and fitness of these agents and materials must be ensured over the entire period of use. In particular, the high levels of contamination in the washing and sterilization processes and through use must be evaluated.
Process description: Cleaning and disinfecting by wiping
Cleaning is the targeted removal of unwanted contaminants by overcoming the adhesive forces between the contaminant and the surface to be cleaned, and the complete removal of the released contaminants. The efficiency of the cleaning process is based on a combination of mechanical removal by the wiper cover and the chemical action of the cleaning agents. During disinfection, biocidal agents are applied to the contaminated surface to inactivate and kill any pathogenic and product-damaging microorganisms present. For this purpose, the active ingredients must be applied in sufficient quantity to the entire surface to be disinfected via the saturated wipe cover. The prerequisites are valid absorption and consistent dispensing of the active ingredient solution as well as wetting of the surface. The mechanical action during wiping supports the germ-reducing effectiveness.
The cleaning and disinfecting of room surfaces is carried out using the so-called "wet wiping" method. Wet wiping is a process to remove adherent soiling and/or to achieve a germicidal effect. Confusingly, the term "wet" does not mean "dripping wet", but rather the wetting of the surface with a uniform film of liquid. As a rule, the process is carried out in a single step: In this process, the surface is wiped in one step with a saturated wiper cover, and the residual liquid dries off without re-wiping. In the same step, active substances are applied and soiling and residues are carried away by the wiping cover. The one-step method is combined with the socalled cover change method: Each wipe cover is used only once to prevent contamination from being carried over via the covers and, depending on the application method, via the solution used.
As a rule, cleaning agents and disinfectants are used in the GMP environment once their efficacy has been proven. However, the actual efficiency only becomes apparent when the entire process is evaluated. The process description shows that the wipe cover plays a central role here, in close interaction with the preparation or saturating system via which the solution is made available to the wipe cover.

Recommendation
Wednesday, 1 October 2025 13.00 - 17.00 h
Transfer of Analytical Procedures - Live Online Training
Requirement | Cleanliness specific | Process -specific | Application specific |
Fluid absorption capacity and fluid holding capacity | X | X | |
Liquid release capacity | X | ||
Surface wetting | X | ||
Cleaning efficiency, absorption and holding capacity of contaminants | X | X | X |
Surface performance | X | ||
Chemical durability | X | ||
Active ingredient adsorption | X | ||
Particle release and abrasion resistance (saturated wipe cover) | X | X | |
Washing resistance and wear resistance | X | ||
Sterilizability | X | X | |
Thermal resistance | X | ||
Extractable residues | X | X | |
Outgassing (AMC) | X | X | |
Hygienic design and handling | X |
Requirements are influenced by the cleanliness requirements of the room environment, the production process and by the users:
Cleanliness specific | Requirements by the air purity class and surface cleanliness class. |
Process-specific | Requirements imposed by the production process on the cleanroom environment |
Application-specific | Requirements due to the type of application |
Table 1: Overview of requirements due to the general use for cleaning and disinfection in the manual wiping process in the GMP cleanroom, based on VDI 2083, sheet 9.2, tab. 23
Requirements for a GMP-compliant wipe cover
The following tasks for the wipe cover result from the process description:
- absorption of the active ingredient solution,
- transport of the active ingredients to the contaminated surface,
- dispensing of the active ingredient solution and wetting of the surface, and
- carrying away and removal of the contaminants by wash-off and mechanics.
The functionality to perform these tasks is complemented by other application-specific properties such as chemical resistance and surface performance. In addition to the properties resulting from use in the wiping process, wiping covers themselves must not be sources of contamination and must not promote the accumulation of microorganisms. The totality of all requirements is also described by the term "cleanliness suitability", which specifies that a wiping cover must be suitable for the respective use and process in the respective cleanroom1.
Since the use depends on the company-specific cleanliness requirements, processes and uses, the requirements for the wipe cover must be defined by the user for his area of application. For the GMP cleanroom, however, it is possible to assume a performance profile as standard, since many requirements for wipe covers are specified on the basis of the applicable regulations. The specification and qualification of a GMP-compliant wipe cover is based on the EU GMP Guide, the standard DIN EN ISO 14644-5, the guideline VDI 2083, sheet 9.2, and various textile testing standards (including the DIN EN ISO 9073 and IEST-RP-CC-004.3 series of standards).
Process reliability through validation
Validation provides documented proof that the cleaning and disinfection process actually leads to the expected result in a reproducible manner. Process reliability in cleaning and disinfection using the wiping method is achieved when
- the liquid absorption of the wipe cover is constant and reproducible; prerequisites for this are a valid preparation method or saturation system and a valid liquid absorption capacity of the wipe cover,
- the surface is uniformly wetted with a continuous liquid film, which requires a constant liquid release capacity of the wipe cover,
- a release of microbial agents in sufficient quantity to the surface, taking into account possible agent adsorption, and
- complete entrainment of all contaminants without carryover (cleaning efficiency),
- the compatibility of wiping textile and chemistry is given, i.e. the evaluation of a possible active substance adsorption and testing of the chemical resistance,
- the efficiency and stability of the working solution over the service life, and
- the hygienic safety of the entire process is given, as well as
- the typical signs of aging and wear of the wipe covers and the operating materials that are reprocessed for reuse are taken into account.
Evaluation of process safety with regard to aging
Application with chemical agents, abrasion in use, interactions with residual soiling and residues, and reprocessing operations can negatively affect the textile structure and thus the functionality of wipe covers and thereby reduce the suitability of a wiper cover over time. Material fatigue and material breakdown also pose the risk of undesirable release of fibers and filaments from the textiles.
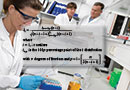
Recommendation
7/8 October 2025
Practical Statistical Tools for Analytical Laboratories - Live Online Training
Due to the changes that cannot be ruled out as a result of regular loads and the associated wear, a reusable mop cover can become a contamination risk. Therefore, the maximum duration of use must be determined by the number of reprocessing cycles. Based on studies2 and empirical values from industry and cleanroom laundries, recommendations are available for the number of application cycles for reusable wipe covers. The aging phenomena evaluated here were caused by influences that are generally to be expected in a GMP cleanroom. However, this recommendation does not release the user from an individual suitability and compatibility test and, if necessary, from adapting the application cycles to specific application conditions.
Conclusion
Reusable wipe covers GMP-compliant and process-safe in use, in summary, means that they must be qualified for the intended use with regard to the requirements of the GMP regulations, must not pose any risk of contamination, and must ensure safe implementation of the processes "cleaning" and "disinfection" through the given functionality over a defined period of use. The evaluation of the wipe cover is part of the disinfection validation and thus of the contamination control strategy.
About the Author
Margarete Witt-Mäckel has been working as a coach and consultant in hygiene and quality management since 2012.
Source:
1 VDI 2083 Blatt 9.2 (2017). Reinraumtechnik – Verbrauchsmaterialien im Reinraum. Berlin: Beuth.
2 Schmeer-Lioe G, Witt-Mäckel M et al (2016). Wiederaufbereitung reinheitstauglich! Analysen zur Alterung von Mehrweg-Wischbezügen für Reinraumanwendungen. Reinraumtechnik 05/2016, S. 48–53. Weinheim: Wiley-VCH.