Quality culture
If we apply Simon Sinek's Golden Circle (WHY? HOW? WHAT?)1 to a pharmaceutical manufacturer, then the needs of the patients correspond to the WHY, the GMP requirements to the WHAT and Quality Culture to the HOW.
Quality Culture thus represents the link between the WHAT and the WHY. It has a significant influence on HOW a pharmaceutical company fulfils the needs of patients and how economically successful it is in doing so.
Every company has Quality Culture per se, which varies from company to company. The quality of a company's quality culture can be quickly recognised and influenced by three of the most important characteristics of Quality Culture - dealing with conflicting goals, with errors and with key figures.
Helpful handling of conflicting goals
The Corona pandemic has drastically shown us all that, in addition to quality, the ability to deliver urgently needed products is also important: medical protective equipment, medicinal products, hygiene products, etc. In addition to these two target variables of customer needs, the third target variable in every ( manufacturing) company is profitability: if the quality of the product produced meets the requirements, the company can deliver the product and thus make a profit.
However, the people employed in different areas and hierarchical levels in a company usually have very different perspectives on these three target variables due to their functions.
- The employees in the GMP areas are very strongly focused on quality (products, processes, systems, etc.) through extensive and permanent GMP training. They are also responsible for meeting completion or delivery deadlines. However, the topics of efficiency and cost-effectiveness appear very little in training topics, or only for a few.
- Managers in the GMP areas are measured above all by their adherence to deadlines and production quantities. They also have to pay attention to economic efficiency, especially budget compliance, and they are responsible for ensuring that no quality problems occur.
- The management and senior management are primarily responsible for the economic success of the company. They are informed about the delivery situation and quality issues in the management review.
- The support areas (personnel, IT, finance, etc.) are often measured by key figures that have no direct or indirect relation to product quality or delivery quantity. Their indirect contribution as support for the operational areas and thus also on delivery quantities and deadlines as well as on the quality of the products and systems, is therefore often not conscious in everyday life and individually very differently pronounced.
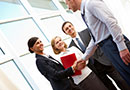
Recommendation
10/11 September 2025
Qualified Person Education Course Module A - Live Online Training
These different perspectives result in more or less major conflicts of objectives. A good quality culture therefore needs a helpful way of dealing with these conflicting goals:
- Everyone has clarity about the most important criteria of the three targets: quality, delivery capability and profitability.
- Everyone is clear about the needs of their external and internal customers.
- All have clarity about their own contribution to the success of their internal customers.
- (the WHY of one's own activity).
- All owners, designers, authors of systems, processes, documents have helpful knowledge for robust and efficient systems, processes, documents.
- All have consensus that optimal solutions can only be found together.
In dedicated team meetings and training sessions, this clarity and knowledge is jointly developed and communicated.
Employees have a good sense of whether management guidelines and the daily decisions of the executives are in line with the comprehensive GMP guidelines, quality requirements and goals or not. Any discrepancy can quickly lead to demotivation and indifference to GMP requirements, with sometimes fatal consequences for GMP compliance and data integrity. All managers should therefore be aware that they play an important role in Quality Culture and, as credible role models, make consistent and motivating decisions for employees on quality in line with profitability.
Dealing with mistakes in a helpful way
To err is human. It is also quite human to look for someone to blame for mistakes and thus to accept human error as the cause of deviations. However, premature blame often prevents the real causes from being recognised.
A helpful way of dealing with errors is to recognise human weaknesses as such and to take them into account when creating robust processes, systems and documents. This is the only way to create suitable framework conditions so that employees (including executives and management) in all areas of the company can do their jobs right the first time by acting in a quality-conscious manner (Do IT RIGHT THE FIRST TIME).
According to our approach "People will always make mistakes; however, the resulting consequences (deviations, accidents) are avoidable!"
A human error is only the consequence of underlying causes and the human involved is, according to our principle of the innocent trigger, only a participant in the cause-effect chain. This view and the system we have developed with 5 levels of causality (Fig. 1) help to recognise the deeper, true causes of a deviation or an event. On this basis, effective and sustainable, cause-oriented measures can then be derived that can prevent a recurrence of the same error, an occurrence of similar errors or an occurrence of the same kind of errors.
According to this system, there are two categories of measures:
- Correction to eliminate the discrepancy (deviation, OOS, etc.) and its consequences.
- 3 Types of Preventive Actions
- Therefore, instead of CAPA (Corrective Action and Preventive Action), we now use and recommend the more appropriate term CaPA (Correction and Preventive Action).
Explanation: Measures that are intended to prevent a recurrence of the same defect at the same location have so far been referred to as Corrective Actions. However, logically they are Preventive Actions.
In addition to a risk-based approach, we have developed a target-oriented, universal Root Cause Analysis (RCA) tool for carrying out a root cause analysis. It contains what we consider to be the three necessary requirements for a complete RCA tool:
- 1. the recording of the (chrono-)logical sequence of relevant circumstances
- 2. the listing of possible causes and
- 3. the systematics for the presentation of interrelationships and results (especially for regular evaluations) also for cases where more than one root cause is found
Fig. 1: 5 Causality levels with CaPA concept (Correction and Preventive Action)
The popular 5xWhy tool only fulfils the first requirement and also carries the risk of assigning blame to the persons involved. Therefore, we strongly advise against using this tool.
Systematic causes behind an individual case (e.g. inadequate qualification of SOP authors) are usually only recognised by investigators if they have cross-divisional experience or knowledge. Even deeper (quality) cultural causes can usually only be identified with the help of suitable quality culture assessments (e.g. RIGHT concept by KU-Pharma2).
Not only those directly involved in an event should learn from the mistakes. Effective communication and information to others is therefore essential. Error evaluations are particularly helpful as part of the qualification (e.g. "Technical Writing", "Process Quality by Design") of process designers (e.g. SOP authors), investigators, QA, QP and managers. Basically, managers should inform their employees about the events in their area of responsibility, the findings from the investigations and about the measures that have been defined. This accomplishes three important tasks at the same time:
- 1. sensitise employees to sources of error,
- 2. to create trust and motivate employees to report all errors openly without fear of being blamed or even sanctioned, and
- 3. to strengthen team building by emphasising error prevention as a common goal or by finding new solutions together.
Helpful use of key figures
Key figures are intended to make work performance, quality and even abstract strategies quantifiable. In addition to process and business management ratios, quality ratios are playing an increasingly important role in pharmaceutical operations.
Authorities now also want to use key figures to ensure the supply of medicines. In response to the increasing number of supply bottlenecks for medicinal products in recent years, the German Bundestag passed amendments to the German Medicines Act (AMG) on 13 February 20203. This introduced an obligation for pharmaceutical companies and pharmaceutical wholesalers to report available stocks, production and sales volumes. The U.S. Food and Drug Administration (FDA) already issued a draft guideline on the transmission of quality indicators in November 20164. In this way, the authority wants to establish risk-based monitoring of manufacturing plants and identify supply bottlenecks in good time in order to be able to counteract them if necessary.
The introduction of key performance indicators is a critical step from the perspective of quality culture, because there are a number of things to consider. Targets and indicators should be defined SMART (specific, measurable, attractive or accepted, realistic, scheduled) and the employees should be able to influence the achievement of the targets themselves. Tragically, the "guilty party" is automatically found if an agreed goal is not achieved. A good quality culture is characterised by a fair and open analysis of the causes. This is because priorities for tasks, projects and goals often change during the implementation phase or additional tasks are added that put a strain on the available resources.
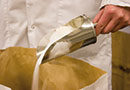
Recommendation
16/17 September 2025
EU GMP-/FDA-compliant Sampling - Live Online Training
A helpful way of dealing with key figures and goals also includes managers communicating to employees the WHY of the respective goal. It is particularly important to understand HOW a goal is to be achieved, i.e. which strategies are desired and which strategies are not allowed. Especially under unfavourable conditions, strategies (e.g. shortcuts) can otherwise be developed to achieve the goal, which, out of intention or self-defence, consciously or unconsciously, can in the worst case lead to serious data integrity problems or GMP violations.
If the WHY of a metric is not known and/or the HOW is not defined, two specific effects are often observed: an erosion of objectives or a strategy substitution. Example: After 30 days, at least 95 % of the deviation investigations should be completed, i.e. the causes are identified and measures are defined. Erosion of the target means that, for example, the deadline is extended to 35 days in principle, on the assumption that the 30 days were set "arbitrarily". However, the deadline is used to prioritise processing in order to learn from the deviation as quickly as possible to prevent further mistakes. Strategy substitution occurs when the investigation is no longer carried out carefully enough to achieve the target of the indicator. As a result, the true causes are no longer recognised and often ineffective or quickly definable measures (so-called bogus solutions, e.g. retraining) are defined. This new strategy for achieving goals then takes the place of the original strategy for learning from mistakes.
Summary
Quality Culture is characterised by the interaction of rules, measures, behaviour, goals, strategies, etc. Individual criteria have a greater influence on Quality Culture than others. Three of the most important characteristics of Quality Culture - dealing with conflicting goals, with errors and with key figures - make it easy to recognise and influence Quality Culture of a company: so that the quality, delivery capability and profitability of a pharmaceutical company are achieved for the benefit of the patients.
About the Authors
Dr Thomas Krieger
... is founder and CEO of KU-Pharma and works as a management consultant and Qualified Person.
Daniela Krieger
... works as a systemic management consultant at KU-Pharma.
Source:
1 The Golden Circle, https://simonsinek.com/commit/the-golden-circle
2 RIGHT Concept; https://www.ku-pharma.com
3 Act on Fair Competition between Statutory Health Insurance Funds (GKV-FKG) of 22 March 2020; Bundesgesetzblatt, Volume 2020 Part I No. 15, issued in Bonn on 31 March 2020
4 FDA: (Draft) Guidance for Industry: Submission of Quality Metrics Data, Nov. 2016 https://www.fda.gov/regulatory-information/search-fda-guidance-documents/submission-quality-metrics-dataguidance-industry