QUALITY BY DESIGN: THE REINVENTED WHEEL?
ICH's QbD considerations resulting in the respective g u i d e l i n e ICH Q8 describe a rational way for pharmaceutical development of drugs. The balance between rationality and pragmatism, however, seems to be not yet fully recognized in pharmaceutical industry's perception.
Some of these misperceptions are assumed to be based on a lack of looking back into regulatory or scientific history. FDA already published the "Guideline on General Principles of Process Validation"1 and requested "adequate product and process design" in 1987 (23 years ago!).
The "newly" introduced terms like QTPP (Quality Target Product Profile), CQA (Critical Quality Attributes), CPP (Critical Process Parameters), DoE (Design of Experiments) and Design Space are on the first view perceived as additional regulatory burden one has to integrate into existing processes because "authorities want to see it" in the filings.
On the second view, however, people concerned with pharmaceutical development are to realize that these terms describe only what common sense has already dictated in the past as well.
Wasn't it always a problem to obtain clear targets for pharmaceutical development? What should the tablet look like (size, shape, colour, weight), what package is desired (blister, bottles etc.), what product shelf life / expiry date is acceptable in the countries the product will be marketed in later on?
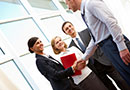
Recommendation
Hamburg, Germany10-12 March 2026
Qualified Person Education Course Module A PLUS IMP Pre-Course Session
All these questions could have also been answered in the past, once the need and thus the impact on development cycle times would have been recognized. If the developer could not get through with his/her well founded request for getting this key information at the beginning of the development activities in the past, why not to welcome ICH Q8 as support in getting these data earlier (even if only under the current regulatory "pressure") and thus enabling us to improve structure of development activities targeting on shorter development cycle times?
QTTP in this sense means a prior written commitment of all the multidisciplinary parties involved in product development to what the later product should look like. "Banal" aspects like tablet color have now to be addressed from the very beginning and thus preventing project completion suffering from time consuming development loops later on (when anybody changes his mind with regard to "such a simple aspect like colour"). Feel reminded to "right-first-time" principles?
The FDA "Guideline on General Principles of Process Validation" says: "quality, safety and effectiveness must be designed and built into a product" and "quality cannot be inspected or tested into the finished product" and "during the research and development phase the desired product should be carefully defined" and "it is important to translate the product's characteristics into specifications as a basis for description and control of the product.” Feel reminded to the wording of ICH Q8?
CQAs have actually always been the base for setting specifications, since the critical product features are those to be kept well under control. The FDA Guideline requests "to evaluate all factors that affect product quality". Feel reminded to risk analysis methodologies to identify "critical" attributes?
CPPs are those process parameters having a significant and thus critical impact on the CQAs. The Process Validation Guideline requests that "key process variables should be monitored", which requires them to be identified before accordingly.
DoE actually means factorial experiments. In 1937 (and thus 74 years ago!) Yates2 already mentioned in "Design and Analysis of Factorial Experiments" how this methodology works. It has always been the most efficient and thus economic way for obtaining scientific elucidation of factor impacts and parameter interactions. However, a lot of developers have not made use of this tool since they felt to put a lot of batches to waste. They haven't realized that it was never the intention of DoE to primarily produce batches within any specification but to provide scientifically sound data for setting these specifications.
With nowadays available IT tools (like MS-Excel) it has become much easier to design, evaluate and present the results of a DoE as compared to former times. The methodology, however, has always been efficient, economic, scientifically sound and regulatorily accepted. Feel surprised about not having used this method earlier?
Design Space information is provided by the results from DoE then. The FDA Process Validation Guideline says "test conditions for these runs should encompass upper and lower processing limits" which requires them to be determined beforehand, of course, and "acceptable ranges … should be established … to set up allowable variations". There are scientific papers available from the late 80's, demonstrating how to set up such a range, but the methods were admittedly not yet been called "design space". However, it should not be the name making the game, but the contents, methods and processes.
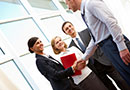
Recommendation
Hamburg, Germany10 March 2026
Pre-course Session: “Investigational Medicinal Products (IMP) QP Education Course”
Keeping the history of regulatory requirements in mind as demonstrated here by the FDA "Guideline on General Principles of Process Validation", it is surprising that ICH Q8 is frequently perceived as a "new paradigm", as a "further regulatory burden" and not as what it actually is, namely a supportive tool for making drug development not only more efficient but also more economic by a systematic rather than a conventional (but nevertheless nonscientific) trial-and-error approach.
Author:
Rango Dietrich (PhD, Pharmacist, QP, MBA)
... is Managing Director of PharmDev Innovations, a solution provider in pharmaceutical development and GMP-related projects.
Source:
1 GUIDELINE ON GENERAL PRINCIPLES OF PROCESS VALIDATION, U.S.Food and Drug Administration, Rockville MD, May 1987
2 Yates, F. : “Design and Analysis of Factorial Experiments”, Imperial Bureau of Soil Science, London 1937