PHARMA WATER: SAVING POTENTIAL FOR ENERGY COSTS
In pharmaceutical operations water is a critical element - not only from the quality point of view. Pharmaceutical water in the quality standards Purified Water (PW) and Water For Injection (WFI) is also an important raw material in the manufacture of medicinal products in terms of volume. The GMP compliant production, distribution and storage of PW and WFI is therefore considered at almost every GMP inspection.
Today, another issue is also gaining in importance. The amounts of energy which are necessary for the production, distribution and storage, cause significant operating costs. At the same time, environmental protection and sustainability become increasingly important in many pharmaceutical companies. Thus, a plant's energy efficiency becomes a major issue in the context of an investment decision.
A pharmaceutical water system is almost always in operation. Just for microbiological reasons, a permanent operation (prevention of biofilm) is mandatory. This also means that systems either periodically - e.g. every two hours - produce a defined amount of water, or that they remain in operation through a constant circulation. Today, so-called re-circulation systems allow to operate water and sewage in the recirculation mode, i.e. in the circuit. However, the cost for this "non-productive time" is significant. It is therefore desirable that pharmaceutical water systems allow a maximum power control. In the WFI production distillation plants can frequently be controlled between 50 and 100% of the performance. In RO systems this effect can be achieved e.g. by a frequency converter at the high pressure pump.
To prevent microbiological growth storage systems for purified water are usually operated at around 20 degrees Celsius. This is further supported by ozonisation, UV disinfection systems or by hot water sanitisation. All procedures also have to be evaluated in the context of energy efficiency. In addition to the different investments it is also necessary to evaluate the energy required.
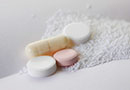
Recommendation
14-16 October 2025
Granulation & Tableting - Live Online Training
More savings are possible e.g. through heat recovery systems for taking advantage of the energy from waste water in distillation plants. The costs for installations like these can quickly pay for themselves. Another approach some water system manufacturers follow is the increase of the overall yield by reducing waste water. Other companies start with the heat loss at the distillation plant. An integrated integrated jacket preheating is designed to reduce the energy loss here. The thermocompression process for the production of WFI - which allows the production of hot, but also cold distillate - is less used (in Europe). In this process no cooling water is necessary. However, the more warm distillate needs to be generated the more the system's advantages decrease.
But there are other costs that need to be taken into account. Here are some examples:
- Cooling costs for an air-conditioned room where the water system is located (in large installations up to 100.000,- Euro and more per year)
- The waste water amounts can vary depending on the system. Some plants consume several times as much waste water as others. It is therefore recommended to also take a look at these plant parameters.
Author:
Oliver Schmidt
CONCEPT HEIDELBERG