Pharma Congress 2022
After two long "pandemic years", the Pharma Congress Manufacturing & Technology finally took place on site again in Düsseldorf Neuss on 31.5.-1.6. A total of 705 participants, 55 speakers and 71 exhibitors had come together to exchange ideas. One major change before the congress moves to Wiesbaden next year has already taken place. For the first time in 2022, the Pharma Congress was 100% international, i.e. all conferences were held in English.
However, in the conference "Facility and Technology Projects", the former "Pharmatechnik-Konferenz" (German; Pharma Technology Conference), everything still revolved around investment projects, i.e. construction and conversion projects of recent years.
Thomas Zlabinger kicked things off by reporting on Boehringer Ingelheim's Large Scale Cell Culture (LSCC) project in Vienna. In his role as validation manager, he was responsible for the execution of all related commissioning and qualification activities. A total of five new buildings were constructed as part of the impressive €700 million project: the LSCC Main Building, a Biopharma Logistics Center, a Quality Building, a Power Supply Building, and a Fire Station. Mr. Zlabinger called it the "new landmark of Vienna." In total, more than 40 individual building permits had to be issued by the authorities, digging at the site accounted for 6900 truckloads and 10 tower cranes were required.
A challenging aspect of the project were the three rail tunnels that run under the new buildings and the vibrations this created, which had to be taken into account during all phases of the project.
The new logistics center includes several storage areas. The 20 °C high-bay warehouse offers 4000 pallet spaces, cold storage at +2/+8 °C with 450 spaces, and underground deep-freeze warehouses for -20 °C and -70 °C with 300 and 50 pallet spaces, respectively. Sampling and weighing is carried out in ISO classes 8 and 7.
The building for the quality unit (QA and QC) has a floor area of 2000 sqm and a usable floor area of 13,000 sqm including a terrace on the 2nd floor. The quality building required attention to two of the railroad tunnels at once, one directly under the building, and one running along the side.
The LSCC main building is a Biopharmaceutical Multiproduct Facility and is served by the Boehringer Ingelheim Launch Plant in Biberach. There are 2x80 L, 4x 400 L, 4x 2000 as well as 6x 15,000 L fermenters available as well as space for others.
Mr. Zlabinger mentioned the many utility systems needed for GMP production. For media and utilities alone, 60 km of piping were laid. Two 20 m3/h PW generators and two 7 m3/h WFI generators are available for water supply.
The cleanroom classes of the total of 414 cleanrooms include CNC (Controlled, not classified), ISO 8 (D) and ISO 7 (C). An elevator in the building in cleanroom class ISO 8 is also in use. For the main building, 4 ventilation systems are in use, two in the basement and two on the top floor. Mr. Zlabinger also discussed the qualification of the premises. The sequence was established: IQ, OQ (technical), basic cleaning, OQ (classification) and PQ. A complicating factor was that the global Boehringer Ingelheim guidelines for cleanroom qualification changed during the project. According to Thomas Zlabinger, in order to keep the extra work under control, it was possible to use the HeRo software, which he had programmed himself. As a result, efficiency in the creation of planning documents increased by 77%, and in the creation of reports by as much as 97%. Transition monitoring could also be avoided, resulting in a saving of about 33% of microbiological samples.
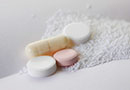
Recommendation
14-16 October 2025
Granulation & Tableting - Live Online Training
In their joint presentation, Dr Daniel Minör (Senior Manager Production at IDT Biologika) and Dirk Steinhäuser (Glatt Ingenieurtechnik) reported on the new vaccine production at a facility in Dessau. The initial situation was the increase in demand for viral vaccines. The goal was to build a flexible multipurpose facility for the production of recombinant live viral vaccines and gene therapeutics, which would be established in less than four years (until the manufacturing license was obtained). It was clear from the outset that there would be increased reliance on single-use technology, both downstream and upstream.
The project was implemented as a fast track project. Time in construction could be saved by using precast concrete elements and by simultaneous construction and commissioning activities on different sides of the building. The required flexibility was achieved by means of four flexible production units in a house-in-house concept. The cleanroom zones of the four areas can be flexibly changed from CNC to C to B.
Ultimately, a time for construction and commissioning of 20 months was achieved, the total time was only 24 months with an investment sum of 23 million euros. The new production building for manufacturing under Biosafety Level 2 (BSL2) contains approximately 900 m2 of class B and C cleanrooms. Interestingly, a Class D was omitted, and entry to C is directly from the CNC area. The authority had no problems with this, according to Dr Minör. However, the introduction of a class D is also possible without any problems. What was difficult, due to Covid, was the delivery time for the single-use production equipment, Dr Minör concluded. But that, too, was successfully resolved.
CSL Behring's "Brownfield Project" in Marburg was also about expanding capacity. In this case, an expansion of the freeze-drying capacity, because the 10-year forecast had indicated a bottleneck in 5 years. Also, a utilization of the production capacities of more than 80% was to be avoided, including the times for shutdown or maintenance. Matthias Klein (member of the Site Operations Leadership Team) and Steffen Mörler (Deputy Director Project Excellence) were the speakers. Matthias Klein opened his presentation by saying that there were a total of four options for responding to the forecast bottleneck. Weighed against each other were a new building, the use of external suppliers, a "do nothing" option, and the aforementioned brownfield project planning, i.e., a capacity expansion at the Marburg site, which was ultimately chosen. In addition to cost and time, the use of the already existing modern filling lines was also a crucial factor in the implementation of the project in Marburg.
The goals were fully automatic loading of the freeze dryer, approval in the EU and USA, and one bulk batch per load at approx. 500L drying capacity. According to Matthias Klein, it was also important to avoid shutdown periods in order to be able to continue production in the building. Difficult, because the new space is in the middle of the 3rd floor of the production building that is in operation. Also, the accuracy of the existing building plans was not known which was problematic given the simultaneous space constraints of this remodeling project. This was solved by laser scanning the building and creating a 3D model, explained Steffen Mörler. In this way, collision checks could be carried out, which prevented problems when bringing in the new freeze dryers, for example. These were brought in through an opening in the building from the outside. This could be accomplished in one day, as could the removal of interfering ventilation ducts. Another key point that contributed to the success of the project, both speakers agreed, was the early involvement of operational production staff in the project. They were involved from layout planning to mock-up, which meant that no design changes were required after the detailed design. The project was successfully completed as planned after 32 months and seven PPQ batches.
Dr Markus Weigandt, Executive Director Pharmaceutical Technologies at Merck, began his presentation with Merck's pipeline. Phases 1-3 include oncology, immunology, neurology and other drugs - sterile as well as solid forms. And this is constantly changing, Dr Weigandt said. So it's difficult to predict what production technologies will be needed in five years. But for the task of setting up a modular GMP facility for clinical trials, this is definitely important. The need for isolators to be able to manufacture the OEB 3/4 and 5 products in the pipeline was foreseeable. In addition, future technologies such as continuous manufacturing and paperless production should also be taken into account, as well as space for QC analyses. A crucial question needed to be answered: would all this fit on the 4th floor of the development building already erected in 2012 at the Darmstadt site? The 1200 m2 available are also separated by a firewall and contain two building cores with staircases, only one of which has so far provided GMP access.
The answer is "yes, it fits". A ballroom concept continued to be weighed against dedicated rooms per unit operation. The disadvantage of the dedicated suites is of course the lost space, due to the airlocks needed per suite. However, the ballroom's disadvantage of not being able to use the rest of the room when using a manufacturing unit then outweighed this, so Merck decided on four separate production suites. Three suites for the production of solid forms (called Solar Suits) and one suite for the production of parenterals (Lunar) were built. The expansion was carried out in partial steps, but access was always from the outside of the building. In the first step, the production suites Solar 1 (coated tablets) and Solar 2 (for new technologies) were built. The Lunar Suite for parenterals was started about one year later, and Solar 3 (conti) and Solar 4 (melt extrusion) were started in a common suite even before the PQ of the other suites. The Solar units are connected by a central Clean Corridor. Media Supply and Engineering sit above clinical production on floors 5 and 6. Merck chose Class C for the isolator environment in the Lunar Suite.
Flexibility is a key aspect in development and clinical sample manufacturing. Thus, 12 different manufacturing paths for coated tablets are possible in Solar (sieving, granulating, mixing, tableting, coating). Granulation is possible by fluid bed or dry granulation. It is already quite full, added Dr Weigandt, but there is still room, for isolators, for example. The production of highly active drugs is designed for OEB 5. This is made possible by completely closed systems during production and transfer until decontamination. The secondary containment is the room which is operated in negative pressure. Exhaust air is cleaned via H14 filters.
Qualification was based on four separate pillars: cleanroom, ventilation system, cleanroom monitoring system and process equipment.
Sustainability was also important in this project for Merck, as it was for Dr Weigandt. For example, the CO2 footprint was kept low by integrating the new clinic manufacturing into the existing building. Also, future routes for production transfers are short. Development and GMP clinic sample production sit in the same building, Commercial Manufacturing is across the street.
Boehringer Ingelheim's presentation focused on the construction of a new launch facility for solid dosage forms. The speakers Volker Glück (Boehringer Ingelheim) and Ilka Rudzio-von Arx (Pharmaplan) jointly presented the 90 million investment project. The starting point for Boehringer Ingelheim was the need for a global launch site. The Solids Launch Facility (SOL for short) was realized with an area of 3200 m2 and two production lines (A and B) in Ingelheim.
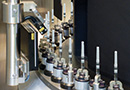
Recommendation
Vienna, Austria21-23 October 2025
Visual Inspection of Parenterals PLUS Pre-Course Fundamentals of Visual Inspection
Production is on the first floor. A mezzanine floor contains the media distribution, and the ventilation systems and offices are located on the upper floor. The exhaust air unit sits on the roof to save space in the technical area for later installations.
Production line B is designed for small-scale production of highly potent drugs in OEB4, i.e. 1-10μg. Isolators (weighing, IPC, tableting) as well as closed containers and systems with e.g. butterfly valves serve as primary containment. Class D rooms form the secondary containment with positive pressure in the airlocks (+) and the surrounding corridor (++). Process and wash water from the WIP systems is collected and directed to separate tanks for noncontaminated and contaminated water.
Digitalization was also important for the SOL project. In addition to an MES, a Room Information Systems (RIM) and a Media Information System are in use. With the system developed by Boehringer Ingelheim, the room signage has gone digital and is connected to the MES. The logbooks are also digital, as is a training system (called "Virtual Helmut").
In terms of sustainability, the two speakers cited the ramping down of air exchange rates during non-production periods, heat recovery systems, and local sourcing of equipment whenever possible. It's worth mentioning that Ingelheim is a wine region, so wine tanks from local suppliers are in use for water disposal.
John Honey (Head of Engineering) and Alois Probst (Project Engineer) from Roche in Penzberg spoke of project work at a particular speed. The driving force was the Covid pandemic and the greatly increased demand for Roche as a supplier of PCR tests. Short-term measures such as shift work, seven-day weeks and overtime were not enough to cope with the situation. In order to make the necessary contribution in the fight against the pandemic, more than 20 projects were started per year and more than 60 projects were processed simultaneously with an annual CAPEX of 200 million euros. John Honey and Alois Probst explained the EMGP2P project as an example. This is the expansion project for the production of magnetic glass particles (MGP), which are required for PCR tests and are produced exclusively in Penzberg. Time was of the essence, emphasized John Honey. The goal was to complete the project as quickly as possible and in less than a year. It was clear, added John Honey, that this would not work with the classic "milestone" approach.
There was no time for a new building, so a suitable space within the site had to be found for the expansion. Project approvals also ran tremendously fast. For example, Friday funding requests were approved as early as Monday, a process that can otherwise take weeks. Ultimately, two factors led to success: the project strategy and the project team, meaning communication and mindset.
Parts and equipment with long delivery times were ordered early and at risk, often based only on preliminary planning. Orders were often placed when specifications were only 90% finalized. For example, HVAC equipment was ordered in a design that was clear it would not fit. Adjustments to the planning were not addressed until after the order was placed. Suppliers were thus brought on board as early as possible, and penalties for late delivery were often not formulated. However, due to the importance of the "pandemic" projects, resources were diverted from other Roche projects. Overall, the speed added about 15% to costs.
The planning phase or meetings were purely virtual. Also, no unnecessary meetings were held. For example, there was only a short daily meeting, with additional meetings only when needed. Project documentation was available to the team on a cloud-based system. The open error culture was important. It was clear to management as well as the team that some decisions could be wrong. What was important then was the fix not the finger pointing. The key was to keep the team motivated by the one, common goal: we were fighting the pandemic. We wanted a productive plant, not a perfect one, John Honey explains. The pandemic has changed the way we work.
Outlook for 2023: On March 28-29, 2023, the congress will be held for the first time at the Congress Center in Wiesbaden.
About the Author
Dr Robert Eicher
... is Operations Director and organises and conducts courses and conferences on behalf of the ECA Academy around pharma technology.