ICH Q10: IMPLEMENTATION THROUGH TOTAL PROCESS QUALITY IMPROVEMENT
Roadmap from GMP to modern Life Science Quality Systems
Part II: Product Lifecycle process performance control through Metrics Based Quality Surveillance.
Part I of this paper (Koch, 2013 - see GMP Journal issue 11 from October/November 2013) describes the changes needed for proper implementation of ICH Q10 objectives using transformative (Deming) quality cycles to lower the gap between management expectations and operating performance. The gap in the mind-set at different organizational levels can be explained looking into the hypothetical evolution of quality in an organization (figure 1). During the start-up of an organization, all expectations and tasks are clear and everyone is highly committed. The quality drive is pathogenic. During growth, a reactive attitude and drive is promoted mainly from the Quality organization, with a focus on compliance with regulatory expectations. Increased organizational maturity leads to increased oversight by implementation of a systematic quality drive and statistical tools are applied, and lagging metrics are installed for performance measurement. Upon evaluation of performance results it is concluded that if costs and quality have to be managed properly, a pro-active attitude and a quality culture is required. The organization becomes adaptive and the QA role is inter-active reaching out to operating excellence.
The change in mind-set contributes to a desired Quality Culture wherein transparency to learn from mistakes is key (Sam, Koch, 20141). Process ownership and quality metrics surveillance is based on performance management of both lagging metrics, and focussing on strategic objectives using leading metrics and QA governance. The highest level of organizational maturity (operating excellence) will be achieved in a cross functional driven and adaptive organization with inter-active QA functioning. The awareness of quality ownership is intrinsic in each individual.
The actual problem that we are facing in life science industry is that the quality drive in the mind-set of our executives is preached to be pro-active whilst in practice the organizations capability is limited with a systematic quality drive. The required tools are available but neither fully implemented nor embraced. In practice the GxP compliance driven environment created a reactive culture which is not ready to adapt. This is why the quality culture has become such a hot topic and struggle for pharmaceutical companies.
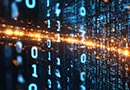
Recommendation
Copenhagen, Denmark26 August 2025
Raw Data - Understanding, Defining and Managing
Fig. 1: Hypothetical evolution to organizational maturity
The initiative of the US Food and Drug Administration (FDA) on the Vision for 21st Century Manufacturing is to obtain an objective measure on the quality of products or processes and the quality of sites creating a pharmaceutical sector that can reliably reproduce high quality drug products with minimal regulatory oversight (Janet Woodcock, speech at ISPE Conference, November 6, 20132).
It is to the author's strongest opinion that quality should support the business and pay-off. A quality metrics surveillance model should not only fulfil the before mentioned but also support best business. Quality surveillance shall provide objective information for decision making and fulfilment of goals and objectives.
Process understanding, performance and continual improvement
ICH Q10, Section 3.2 states that 'An effective monitoring system provides assurance of the continued capability of processes and controls to produce a product of desired quality and to identify areas for continual improvement (EMA, 20143). The process performance and product quality monitoring system should provide knowledge to enhance process understanding.The approach of a schematic process description for detailing and to evaluate processes 'Suppliers-Input-Process- Output-Customers' (SIPOC) is widely used in lean methodologies. Factors influencing a process description are not limited to regulations or requirements but mostly to the culture in place and common routines (business practice). Considering these actors and factors is important for identification of critical quality attributes (CQA's) upon definition of metrics for continuous improvement. Due to the fact that a process is always dynamic, deviations will occur although within acceptable limits on proper application of Quality by Design (QbD) (figure 2.)
Fig. 2: SIPOC with influencing actors, QbD and metrics application for continual improvement.
Total Process Quality Improvement and Quality Management Systems
In order to apply quality metrics to analyse, monitor and improve products, processes and site quality, we must first identify and order the distinct organizational stages and processes.
As described in Part I of this paper (Koch, 20134) the ordering is performed in two directions:
- Chronological following the Product Lifecycle.
- Hierarchical to include Strategy (executive level), Tactics (establishment level), and Operations (product realization level).
The application of processes at distinct organisational stages imbed the functional management aspects and creates insight about the 'Who, What, Where, When and the How', being essential questions for process control and process improvement (Juran, 19995). The main difference with GxP is that the regulations describe the Do's and the Don'ts only requiring action in case of nonconformities.
TPQI strives, equally to the TQM principles, to enable operating excellence by creating an organization that values and respects people and their creative capabilities. Without transparency and ability to learn from mistakes there is no true continual improvement possible. It is not only about Right First Time (efficiency /cost control) but even more important is doing the right things (effectiveness and patient safety). It is not beneficial to start an improvement pro process (Kaizen) without being able to identify and locate the real problem 'Gemba' (Imai, 19976). Therefore it is of primary importance to realize the 'Why' of taking action. The 'Why' is never to be in compliance but it shall contribute to business improvements and as such to the wellbeing of patients.
What is missing for the pharmaceutical industry is the visualization of a quality model that reflects the business as well as the drivers to promote improvement thereof. For creation of the model all high level quality processes are identified. These processes are reflecting the basic business questions at the hierarchical levels of an organization: Strategy, Tactics and Operations (Koch, 20134). The primary business quality drivers steer the main quality processes at the strategic level (process owners: executive management), and at a tactical level (process owners: accountable management for the establishment of a company). The operational quality processes follow the product lifecycle for product realization (process owners: R&D managers, Production managers and QA managers) completing a coherent framework (figure 3).
Fig. 3: Framework for the quality model including the main quality processes
Following the product lifecycle, the quality processes for product realization follow the chronological phases from R&D to manufacture and post market surveillance. It is obvious that the quality processes at strategic level and tactical level remain independent from the phase of product realization.
All quality processes in the distinct phases of the product lifecycle are controlled by processes that individually or in combination generate Corrective Actions and Preventive Actions (CAPA's). As such these control processes are part of compliance management (see figure 4).
Fig. 4: Product Lifecycle processes controlled through compliance management
All quality processes at the hierarchical levels of an organization are overarched with the documentation processes forming the Quality Management System. All activities are interconnected following the transformational quality cycles (Koch, 20134) and progress and priority setting for decision making is performed at the Management Review.
Imbedding the product lifecycle processes into the framework, a comprehensive Quality Management Model is obtained equipped for continuous improvement of the product lifecycle, quality processes and the QMS. In addition the objectives of the ICH Q12 (concept) on Product Lifecycle Management are included (detailed Product Lifecycle Processes information are available upon request). The complete model is suitable for detailed process identification and to cover all goals and objectives for modern pharmaceutical quality management as intended using ICH Q7, ICH Q8, ICH Q9, ICH Q10, ICH Q11 and expectantly ICH Q12.
Feasibility of lagging performance metrics and leading metrics for business quality improvement
In addition to the operational processes, systems shall be in place to assure and control 'compliance with regulations'. The FDA pharmaceutical quality for 21st Century initiative (Woodcock, 20132), strives for a quality drive and not a compliance drive. As Janet Woodcock (Director of FDA/CDER) stated in her plenary address at the 2014 PDA/FDA Joint Regulatory Conference7: "The best and probably the only way to reliably achieve high quality production is to have everyone involved in their production from shop-floor to CEO be pretty fanatically committed to it at all times, and 'it' is related to high quality not to compliance."
In other words quality is in the lead and compliance is regarded to be an obligatory enabler in the realization thereof. Building in quality is monitored using quality metrics.
The utilization of quality metrics is not new for the pharmaceutical industry as expressed in a case report (Torkko et al, 20148). However, it is remarkable that the use of metrics is limited to (lagging) performance measurement without focus on the improvement of future business quality using leading metrics.
In consultation of the industry on FDA's 21st Century Initiative, the working groups from both the Parenteral Drug Association (PDA) and the International Society of Pharmaceutical Engineering (ISPE) were not successful in proposing a coherent set of lagging and leading metrics that could adequately reflect the status of quality within their business (PDA, 2014 and ISPE, 2014).
The goal is to set up a metrics model that is suitable to assess the quality performance of a site and/or organization as well as to contribute to a quality culture through improved awareness and commitment to business quality. This is performed by analysing the quality processes that contribute to the basics of the establishment reflecting the improvement of the 'as is' situation into the desired 'to be' state of the organization. This is defined as 4 Business Quality Lead-factors (BQL's) to be the pillars representing the established state of:
- The Organization
- Assets /Resources
- Product Realization
- Assurance & Control
On the other hand, the supporting enablers to an organization needed to maintain and improve our established state, are important attributes. Two of them are described in the ICH Q10:
- Quality Risk management
- Knowledge Management.
Additionally 2 enablers are defined to be of eminent importance driving good business and quality culture:
- Change Management (not change control): Those elements of importance to guide and realize major changes in organizations e.g. re-organizations, project management, process and system changes.
- Conformance Management: Putting quality upfront to additionally improve cycle times and capability, and reduce waste and inventory, compliance is no longer the goal to achieve but becomes a mandatory enabler that supports quality achievements and contributes to a desired quality culture.
In total 8 straight forward BQL's are defined to monitor and steer and improve the quality of the business. Each BQL is driven by Critical Quality Attributes (CQA's) monitored using Leading Metrics. The Leading Metrics are again based on the monitoring performance results measured using Lagging Metrics. The Leading and Lagging Metrics are cascaded to the separate disciplines of the organization. As such a Metrics Model is obtained that drives Operating Excellence of the company (figure 5). Practically, the monitoring results of lagging metrics are linked with other interacting Leading Metrics.
Fig. 5: QBL’s with CQA’s (Leading Metrics and Lagging Metrics)
Quality Risk Management analysing performance results and targeting Management Review.
Cascading Management Reviews into distinct levels and disciplines of the organization, and proper oversight of doing it right, is of great importance to achieve buy-in of the whole organization. The routine application of Quality Risk Management (QRM) is primary for sound analyses of monitoring information and the evaluation of the impact to our establishments:
- Identification of the Failure Effect: The monitoring results obtained from the lagging CQA's are analysed using FMEA and weighed.
- Identification of the Failure Mode: The impact of the failure effect is evaluated at the established level performing an impact analysis of the Leading CQA's.
- Finally, using the Criticality Impact result, objectives are defined for improvement.
It provides objective input to the Management Review and supports senior management in decision making, setting the objectives for the Quality Planning. Following the transformational quality cycles, routine application of QRM provides continuous information reflecting the quality of performance and new leads, both bottom-up as well as top-down (figure 6).
Fig. 6: QRM in performance monitoring evaluation for Management Review
The easy access result of the quality surveillance is depicted in a radar chart, expressing the results of the quality status for each QBL.
Discussion
The aim of TPQI is to improve operating results by lowering the gap between management expectations and the operational capability of the organization.
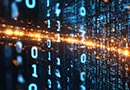
Recommendation
Copenhagen, Denmark27-29 August 2025
Data Integrity Master Class
Enhancement of the pharmaceutical industry can only be achieved through improvement of quality awareness, and commitment and involvement of all people. The application of the provided methodology will support and drive a quality culture that leads to improved business results. As it is with every attempt to improve, all depends on the will, openness and ability to learn from mistakes. The change in mind-set that compliance is no longer the goal to achieve but regarded as a (mandatory) tool to direct the realization of effective and safe medicinal products. Optimal performance is achieved by striving towards operating quality excellence and maximization of the business result and shareholders value.
The author is in contact with a software institute to investigate the possibility for routine monitoring and reporting on a consistent and validated basis. For information and questions: hmpkoch@qimp.nl
Author:
Henny MP Koch
... is consultant in the Life Science Industry. His company, Qimp Management Systems Ltd. focusses on sustainable improvements and business solutions with reference towards well-being and patient safety. For questions he can be reached at hmpkoch@qimp.nl.
Abbreviations
- BQL Business Quality Lead-factor
- CAPA Corrective Action and Preventive Action
- CQA Critical Quality Attribute
- FDA/CDER US Food and Drug Administration/ Center for Drug Evaluation and Research
- ICH International conference on Harmonization of Technical Requirements for registration of Pharmaceuticals for Human Use.
- ISPE International Society for Pharmaceutical Engineering
- TPQI Total Process Quality Improvement
- TQM Total Quality Management
- PDA Parenteral Drug Association
- QA Quality Assurance
- QbD Quality by Design
- QRM Quality Risk Management
Literature
1 Sam AP, Koch H. Quality Metrics, Quality Culture, Quality Matters! Industrial Pharmacy Issue 44 December 2014 p 18 - 22.
2 Woodcock J (FDA/CDER), speech at ISPE Conference, November 6, 2013.
3 EMA (European Medicines Agency) ICH Q10 Pharmaceutical Quality System, EMA/CHMP/ICH/214732/2007, 14 May 2014.
4 Koch H. Total Process quality Improvement for implementation of ICH Q10 including control of performance metrics for Management Review. Part I: Trans formational oversight using quality cycles for ICH Q10 implementation. GMP Journal Issue 11 October/November 2013 p 12-15.
5 Juran J. and Godfrey A.B. Juran's Quality Handbook. Mc Graw Hill, New York 1999.
6 Imai M., Gemba Kaizen The Kaizen Institute Ltd. Deventer Kluwer 1997.
7 Woodcock J, Plenary Address at the 2014 PDA/FDA Joint Regulatory Conference October 2014. Retrieved on YouTube (accessed 28.01.2015).
8 Torkko M, Katajavuori N, Linna A, Juppo AM. The utilization of quality KPIs in the Pharmaceutical Industry. J Pharm Innov. (2014) 9: 175 -182.
Hutchins D. (2008) Hoshin Kanri, The Strategic Approach to Continuous Improvement. Aldershot, Hampshire England: Gower Publishing Ltd.