GMP DOCUMENTATION
1. Introduction
One of the most discussed GMP topics in drug manufacturing is documentation. You are most likely familiar with questions such as
- How are empty spaces correctly devalued (each one individually, each with a signature, is it possible to "X out", etc.)?
- How does one authenticate a copy in compliance with GMP (one signature, two signatures, one signature of a quality unit)?
- Where does it say that no "quotation marks" (ditos) are allowed? And yet (actually) everything is clear.
2. Requirements from the EU GMP Guide, AMWHV and AMBO
The basis for requirements for a GMP-compliant documentation is laid down in the EU GMP Guide, Part I, with its Chapter 4 (Documentation) and Annex 11 (Computer Aided Systems) for documentation with computerized systems. Specific requirements for documents in quality control can further be found in Chapter 6 (Quality Control). Below, the article focuses on Chapter 4, EU GMP Guide Part I (medicinal products), in particular handwritten entries.
What requirements can be found in Chapter 4 of the EU GMP Guide, Part I?
The chapter "Principles" emphasizes that the documentation should be completely defined in the QM system. The possibility of the diversity of documentation (paper, computer, photo) is explicitly mentioned. The main objective of the documentation system is to control, monitor and record with regard to direct or indirect quality aspects. The document refers to a suitable good documentation practice regarding the rules and protocols. Controls are also required to ensure the accuracy, correctness, availability and readability of the documents. These are all requirements that have already existed since the publication of the GMP guideline in the late 1980s. The term "written" defines that the data can be rendered in human readable form.
Under the sub-section "Records" we then find an indirect definition for raw data: they are data that serve as the basis for quality decisions. Raw data should be set (at least for electronic protocols).
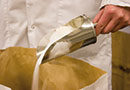
Recommendation
16/17 September 2025
EU GMP-/FDA-compliant Sampling - Live Online Training
In the next section entitled "Generation and Control of Documentation", the guide calls for defined control measures for master documents, for official copies, for data processing and record keeping. Appropriate controls on the accuracy and completeness of the protocols during the retention period should be in place. These specifications have also been existing since the end of the 80s.
Documents should be carefully designed, generated, reviewed and distributed. A reproduction process of original documents should not lead to errors. Documents with instructions should be approved, signed and dated by appropriate and authorized persons, and the date of entry into force should be fixed. Furthermore, documents within the QM system should be regularly reviewed and kept up to date.
Those are the general requirements for documents. Little of it is concrete, except for the requirements for various control measures mentioned above, the error-free duplication process, the regular checking for topicality and the approval, signing (with date) and the specified entry into force of documents with instructions. Who approves, signs and dates is not fixed. For instructions on manufacturing procedures, specifications, sampling instructions, test methods and other quality control procedures, see chapters 2.5 and 2.6 of the EU GMP Guide, Part I. These documents should be approved by the Head of Manufacturing or the Head of Quality Control for their respective areas. Regarding the approval of written operation procedures and other documents, including supplements, the Heads of Manufacturing and Quality Control share the areas of responsibility (EU GMP Guide, Part I, 2.7), with explicit reference to national rules where applicable.
But what about handwritten documentation? There is a separate chapter on Good Documentation Practice in Chapter 4 of the EU GMP Guide, Part I. Those who now hope for detailed information will be disappointed. Three sections (4.7, 4.8, 4.9) describe requirements for handwritten entries of data:
- Clear
- Readable
- Not removable
- Timely
- Traceability
With regard to changes of entries, the signing and dating is required while preserving the readability of the original information. If indicated, the rea- son for the change should be recorded.
These are the rules for handwritten documentation from the EU GMP Guide Part I (Medicinal Products)!
Can we find more details on handwritten documentation in Part II (GMP for APIs) of the EU GMP Guide? Not really. The corresponding passage can be found in Section 6 (Documentation and Protocols) in 6.14. There we can read again about the specifications for the indelible nature of entries, timeliness with traceability of the entry (person) and the already mentioned requirements for correcting entries. To record the reason for the change, which might be necessary, is not explicitly required.
Searching the German Arzneimittel- und Wirkstoffherstellungsverordnung (AMWHV - medicinal products and API manufacturing regulation) in § 10 (documentation) does not help. The Austrian AMBO regulates the change of handwritten entries more strictly. There a justification for changes is mandatory.
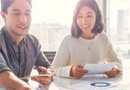
Recommendation
17/18 September 2025
Knowledge Management in GMP - Live Online Training
Pharmaceutical companies have interpreted and tailored these very general rules according to their needs (and sometimes beyond). These company- internal regulations are often specified in a standard operating procedure (SOP Documentation). And as always with interpretations, they can be very diverse ... Many pharmaceutical suppliers have become familiar with them. While company A is completely fine with the supplied documentation, company B vehemently rejects it - and vice versa. The same applies to audits. Depending on your personal background and your own company policy on documentation, audit results may sometimes be different when it comes to questions about (handwritten) documentation.
Could not you possibly "suck honey" somewhere else to be (more) on the safe side as far as (handwritten) documentation is concerned?
3. Interpretation aids for (handwritten) documentation through the PIC/S document PI 041-1 (Draft 3)
In fact, the recently published guidelines, on data integrity can help here. These documents show the state of the art. Outstanding - with 52 pages also in scope - is the draft for a PIC/S document entitled Good Practices for Data Management and Integrity in Regulated GMP/GDP Environments (PIC/S PI 0041-1 (Draft 3) of 30 November 2018. The document is intended to assist GMP inspectors in the context of GMP inspections, and expressly states in the document that it does not provide additional regulatory requirements but provides an interpretation of current GMP/GDP requirements. The topic risk management plays an important role throughout the document. It is important to note that not all data or process steps have the same meaning in terms of product quality and patient safety, and risk management should clarify the importance of data and process steps. Examples for different criticalities of data are provided (e.g. data for batch release vs. cleaning reports in the warehouse). The general basis for the documentation is provided by the ALCOA principle:
- A - attributable (traceable)
- L - legible (readable)
- C - contemporaneous
- O- original
- A - accurate
In principle, this reflects the requirements for good documentation practice in Chapter 4 of the EU GMP Guide, Part I.
With reference to an EMA guideline on GCP inspections in the context of a centralized approval procedure, the document also refers to ALCOA+. The "+" are:
- Complete (complete - also with regard to restoring a procedure)
- Consistent (good documentation practices should always be applied, even in case of deviations and changes of data)
- Enduring
- Available (e.g. for a review)
It gets really exciting in Chapter 8 of the draft, which lists specific considerations on the data integrity of paper documents. Expectations for generating, distributing and controlling data are then listed in tables in 8.4. The three-column table lists in column 1 the sequential number, in column 2 the expectations from the point of view of the authorities and in column 3 potential risks, if the expectations mentioned in column 2 are not met or specific requirements to be controlled. This third column is directed at the inspector and gives advice on what to look for during an inspection. Here are some detailed statements with a focus on (handwritten) paper documentation:
Additional pages attached for completing a document should be identified and signed on the first page - with reference to each page and the number of pages.
Copies must be clearly marked to distinguish them from the original (master) documents. As a possibility, coloured paper or coloured print are mentioned.
Data should not be documented on the back of a document, since those are usually not included in the copying process.
Each blank document must be traceable. The number of empty documents issued is specified in a "bound book". This includes the labelling of each copy as e.g. "copy 2 of 2". If a form needs to be reprinted, this should be done according to a defined procedure and should be justified (rationale, e.g. destruction of the original document) and approved. All output records should be counted and reconciled.
But what requirements are there now for documents to be filled out?
As a general rule, measures should be taken to prevent the contamination of protocols; the protection against wetting is mentioned as an example.
The fact that handwritten entries must be made by the person who carried out a task, actually results from what has been mentioned above. But to check whether the entries are also consistent with the same person has a new quality. This is an example for a claim from this "column 3" recommending a GMP inspector what he should look out for in inspections.
Blank spaces should be devalued, dated and signed. "Ditos" (quotes) should not be used. There should be a uniform date format in the company, protocols should be paginated, and the presence of all pages should be checked as part of an inspection.
For a timely documentation, there is an interesting footnote: the use of a second person recording something for another person should be an exception and should be possible only in the sterile area (for example, when intervening in the filling) or as an aid to foreign-language staff. A supervisor can then make the entries, but he must have seen the process (witnessing). In both cases, both persons, i.e. the person who carries out the activity and the person who made the entry will have to be named in the record. The person who carried out the activity should, whenever possible, countersign the protocol. This is also possible later. In general, such a procedure should be described in writing, and the activities that can be processed that way should be named.
Explicitly addressed is the prohibition of "overwriting", that is, entries that are made in pencil and then overwritten with pens. It should also be noted that some prints fade over time; as mentioned as an example on thermal paper.
Signatures and initials should be individual and not in block letters. Key entries should be signed and dated, in particular if the entries are to be made over a longer period. In that case, not only the last page or the finishing of a process should be signed off on.
The use of stamps / seals should not be encouraged, according to the document. If they are still used, they should be access-controlled. Of course, stamp/seal and those who use them should be traceable.
And what about correcting documents?
Here, the PIC/S document recommends devaluing the incorrect entry only with one line, so that readability is still guaranteed. The use of correction fluids or overwriting is prohibited. A symbol and a date are also required. Interesting is the wording for justifying changes. For critical entry changes, a well-founded reason should be documented and supportive evidence should be available for the change. It is clear that even the changes should be indelible.
When and who should check the protocols ("secondary check")?
Critical process steps in batch records should be witnessed by a designated person (e.g. the supervisor in production) at the time the activity took place. It is expressly stated that inspectors should ensure that the appropriate personnel are available during the manufacturing activities. This is probably because of the "ulterior motive" for "a sufficient number of qualified personnel" (see principles in Chapter 2 EU-GMP Guide, Part I). Furthermore, a review by an authorized person in the manufacturing area are required before the protocols reach quality control. Again addressed at the inspector is the requirement that she/ he should check that every second review was done by suitably qualified and independent personnel (as mentioned, for example, the supervisor in manufacturing or quality assurance). In fact, the requirement for a review and approval of the protocols by a quality assurance unit (Authorized Person / Qualified Person) before release of the batch is self-evident.
Batch records of non-critical manufacturing steps should be checked by the manufacturing staff according to a written procedure after the end of manufacturing. The verification is confirmed with date and name.
Laboratory records containing test results should be reviewed by a designated second person (e.g. another laboratory technician) after the test has been concluded. The review should include the control of all entries of critical calculation steps. Further, the accuracy of the test results in regards to data integrity is to be verified.
There are also requirements for inspectors regarding the review of documents by a second person. They supposed to verify whether this review has been carried out by a suitable and independent second person (e.g. in the production or QA unit).
And how should one handle the printing of simple devices that do not store data (scales, pH meters)? The original print should be signed and dated by the person who generated the printout. So you do not necessarily need a second signature and no involvement of a quality unit.
How do you handle copies of original documents ("true copies")? Related to paper documentation (e.g. reports of analysis results and validation reports) in connection with a "true copy" means that the original document must be archived further on. During the copying process, it should be ensured that no information is lost compared to the original document. Inspectors should review this procedure during inspections, as well. The authenticity of the copy is then verified with signature and date. The document should clearly be recognizable as a "true copy". The recipient of the "true copy" should review the document for authenticity upon receipt. A possible example for such a review would be the verification of the correct signatures. "True copies" should be fi led according to good documentation practice. A distribution list of the persons who received "true copies" should be kept up to date. In case of contracting, there should be an agreement between the contracting party and the contractor about the responsibilities in the course of creating "true copies". This procedure should be audited by the contracting party. Information on the handling of electronic "true copies" as well as on the archiving of documents conclude chapter 8.
Finally, there are some examples of deficiencies in their classification for inspections (critical, major, other). For example, the erroneous transmission of measurement results of "scraps of paper" into a protocol is classified as a "major" finding.
Author:
Sven Pommeranz
... is Operations Director and organises and conducts courses and conferences on behalf of the ECA Academy in the area validation.