Final Version: ECA´s Good Practice Guide Integrated Qualification and Validation
With the "mother of all validation guidelines", the FDA Process Validation Guideline from 1987, the subject of equipment qualification took on a new significance. Suddenly, IQ, OQ and PQ were terms that needed further clarification. With the EU GMP guidelines becoming valid in 1992, the topic of qualification also gained increased importance in the EU (then still EC). However, the corresponding requirements in chapter 3 of the guide were not very concrete. It was a PIC document, then called PH 1/96, that deepened the qualification topic. Other than the US-Guideline, it was also supplemented by design qualification. Starting from the mid to end 90's the qualification requirements for equipment fairly "exploded". The first critical voices warned against "overdoing" ("Validation is not a religious experience or FDA wants McDonalds and we give them Cordon Bleu", Crosson, Campell, Warren, Journal of Validation Technology 08/03). With the coming into effect of Annex 15 to the EU-GMP guideline in 2001, the qualification requirements also became more concrete at EU/EC level. An ISPE "White Paper" from the year 2005 first attempted to counteract this trend and showed where "the journey" to a modern qualification could lead. The ASTM document E 2500 implemented this white paper. With the publication of a draft of the FDA Guidance for Industry, Process Validation: General Principles and Practices in 2008, it became clear that in addition to process validation, the topic of qualification would also change. In the now final version from 2011, there is no longer any talk of DQ, IQ, and OQ, but the term qualification still exists. However, in the US Process Validation Guideline, qualification is integrated into the Validation Life Cycle Concept with its three-stage approach (process design, process qualification and continued process verification). Qualification is now a sub-stage of process qualification and thus a part of the entire validation lifecycle.

Recommendation
30 September / 1 October 2025
Process Validation - Live Online Training
The revision of Annex 15 of the EU GMP guidelines (valid since October 1, 2015) also brought some changes in the area of qualification. The four "classic" qualification levels DQ, IQ, OQ, PQ were in parts defined slightly differently and requirements for User Requirement Specifications (URS) and/or a functional specification were added. Optional Factory Acceptance Tests (FAT) and Site Acceptance Tests (SAT) were also included. Both activities can, if appropriate and justified, be included in the qualification without having to repeat these tests (an exception is if the transport would have an impact on the original FAT test). The specifications for the qualification levels in 'Annex 15 are only mentioned as a possible variant. A reference to alternative approaches? The justified integration of external data sources, e.g. suppliers, is explicitly mentioned.
Fig. 1: Extended Project Life Cycle Model with quality risk management activities
It is precisely this possibility that the final version of the ECA Good Practice Guide "Integrated Qualification and Validation - A guide to effective qualification based on Customer - Supplier Partnership" takes up. A "Task Force" with members from the pharmaceutical industry, plant manufacturers and engineering companies has created the guide. The guide was designed based on the requirements of Annes 15 of the EU GMP guidelines and supplemented by aspects of ASTM Guide 2500. Based on two drafts that were presented at two international qualification conferences and their feedback, the final version will be available in autumn. The final version also includes references to the new "Commissioning and Qualification Guide" of the International Society of Engineering (ISPE) A technical and regulatory review ensures market acceptance. On almost 40 pages, a very compact description is given of how a "lean qualification" can be successfully completed today with the involvement of suppliers. The often nonsensical repeated execution of one and the same test in different qualification phases (FAT, SAT, IQ or OQ) is explicitly addressed. The guide is structured in such a way that it shows the qualification topic from the perspective of a pharmaceutical company (customer) and from the perspective of a supplier. A separate chapter then describes the interaction of the two parties involved. Supplementary chapters on equipment categorization and an overview, which explains in particular the application of quality risk management throughout the entire qualification/ verification process, contribute directly to the applicability.
In a subchapter the integration of process validation into the qualification is explicitly discussed. In principle, this is what was also introduced as an innovation in the FDA Guidance on Process Validation: Qualification and validation are more closely connected. Especially in modern PAT controlled processes, the initial risk analysis can cover both the technical qualification aspects and the process validation aspects as a result of the control strategy for the PAT equipment. An example of a modern process validation including process capability indices is given to illustrate the contents of the chapter. The fact that PQ-tests are possible before ordering a standard equipment from a potential equipment supplier is described as a further possibility of an extended integration of process requirements into the qualification. A completely new chapter gives an outlook on the requirements for electronic qualification documentation. Even if all documents are delivered electronically by the supplier, many companies still print these documents, work with the printed documents and then archive them as paper documentation. Is that still up-to-date? Suggestions on how to deal with scanned qualification documents and which GMP requirements must be met by complete electronic documentation are explained in this chapter. It is a look into the (near?) future of qualification.
The Annexes are very important for the applicability of the Good Practice Guide. They contain sample documents and templates that are successfully used in the pharmaceutical industry and in plant engineering and construction. Be it - in terms of an integrative approach - user requirements coming from the product or the process. Just like a classic user requirement for a piece of equipment. In order to be able to sensibly involve suppliers in the qualification process, they must be suitable - and this must be justified. A separate appendix describes the conditions for this. Furthermore, tables for risk analyses are included as annexes, as well as pragmatic "templates" for project-related changes (Change Management) and deviations. A central document in a joint qualification project between suppliers and pharmaceutical customers is a "Project Quality Plan (PQP)". It controls the documentation requirements and qualification activities on both sides. This PQP is then broken down into test plans. There are sample templates for both documents mentioned above. An example of a questionnaire for the categorization of equipment supplements the separate guide chapter on the same topic.
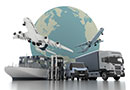
Recommendation
Thursday, 9 October 2025 9 .00 - 12.30 h
Temperature-sensitive Pharmaceuticals – Transport and Vehicle Qualification - Live Online Training
Conclusion: Based on the requirements of Annes 15 of the EU GMP Guide and supplemented by aspects of the ASTM Guide 2500, the final version of the ECA Good Practice Guide "Integrated Qualification and Validation - A guide to effective qualification based on Customer - Supplier Partnership" describes in just under 40 pages what "lean qualification" can look like today. Annexes to the guide with sample documents, which are successfully used in the pharmaceutical industry and in plant construction, ensure direct practical relevance.
Author:
Sven Pommeranz
is Operations Director and organises and conducts courses and conferences on behalf of the ECA Academy in the area validation.