FDA/GMP TRENDS IN THE MANUFACT URE OF ASEPTIC AND SOLID DOSAGE FORMS
On the one side the manufacture of medicinal products are under huge compliance pressure by the authorities. On the other side the pharmaceutical manufacture has to be as cost-efficient today as possible, as the financial scope - e.g. due to rebate contracts with health insurance companies - is constantly getting smaller. For the aseptic production this poses specific challenges. A series of recalls of parenterals by the FDA in the US related to impurities due to particles which were not identified during the manufacture.
Particles in parenterals - the point of view of the FDA
Both the manual as the fully automated visual inspection are done to test parenterals for particles. This subject was discussed comprehensively on the second day of this year's Pharma Congress in Düsseldorf/Neuss end of March. A very important aspect that should be considered as part of the batch evaluation in any case, is the particle identification, if particles cannot immediately be clearly allocated. This was also covered in the presentation by Dr Stephen Langille from the FDA. The allocation and determination of a particle is important in a deviation analysis as well as for process optimisation. However, this does not have to be done by staff during the manual visual inspection. It can be done later. In regard to this there had also been contrary rumours. For Dr. Langille, it is important to identify the critical points in the process and the associated critical control points with respect to the source of particles and their strict reduction: materials, container and container closure, staff and the environment. In his opinion this is the responsibility of the pharmaceutical companies' development as many problems are not explicitly treated here. As he pointed out, sterilisation in the final container does also not solve the problem as sterile particles are not desired either. Another problem for him are frequently the socalled semi-automatic inspections, where the containers to be inspected are passing by the inspector. For him the speeds are often too high to ensure a sufficient examination of containers. When asked, he declined to specify an absolute speed, though. For Dr Langille it is essential that in the qualification at a given speed the particles to be found are actually found. On a question with regard to test kits he replied that sets with real products and particles are preferable. Standard test kits would also be acceptable, though. Both the FDA and the other speakers agreed that following a 100% visual inspection of a lot an AQL random sampling should be carried out.Efficient pharmaceutical production - lean projects
Cost optimisation and efficiency were also subjects that were discussed in one of the conferences. In "Efficient pharmaceutical production" speakers from Boehringer Ingelheim, Vetter Pharma, Takeda and Hoffmann-La Roche presented various case studies. For instance, Dr Andrea Thommet, Operations Manager at Boehringer Ingelheim, covered Boehringer Ingelheim's high-ranking lean project, showing how a lean transformation can take place. A key question toward management at the beginning of a change like this is always: Why? And why lean? For Dr Thommet the answer lies in the numerous changes from both within and from outside which have an impact on the competitiveness - such as continuously changing regulatory requirements, the increasing cost pressures in the health sector, new competitors in the global market but also the expiry of patents. For her it is essential to initiate the pro cess of transformation already during the growth phase, much rather very early in the maturing of a business process than when it starts to stagnate. The lean transformation process is holistic, Dr Thommet emphasised. At Boehringer Ingelheim the focus was on three areas: the operative system, the management system as well as the behaviour. In operations this relates to issues like a better work organisation and the reduction of non value-added activities. In the area of management this concerns things like the introduction of key performance indicators, capacity planning and a systematic personnel development. The third and quite crucial area are attitude and behaviour, i.e. leadership and motivation on-site, e.g. through problemsolving tools. Following, Dr Thommet presented the phase model which served as the model for the Boehringer Ingelheim lean project. In the first about six-month preparation phase, teams were set up and trained. In addition, a milestone plan was designed and the necessary infrastructure was organised. Then the critical phase followed with diagnosis, design and implementation. A total of six months were estimated for this phase. After deduction of sickness or vacation days, approximately five months were left. About six weeks were necessary for the diagnostic phase in which the optimisation potential was determined. Numerous analyses and process observations showed the weaknesses. It is important that detected weaknesses are not seen as failures, but are used for optimisation. The subsequent approximately four-week design phase was used to prioritise ideas and to find solutions for the problems or weaknesses found. These were tested and implemented in the subsequent implementation phase (ten weeks). The last - the stabilisation phase - lasted two years and was supposed to monitor the sustainability of successes. Transparency and the involvement of all staff up to the line were very important in the entire project. Changes always lead to existential fears. Thus one of the first questions pinned on a question wall was: "Is my workplace safe?" Here it is important again to already do a lean project in the growth phase, Dr Thommet repeated, because then the result is not the loss of job, but new jobs in the company.
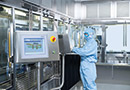
Recommendation
Cologne, Germany21-23 October 2025
Lyophilization 2025 - Includes Workshop at GEA
Trends in the production of solid dosage forms - Sourcing
Various case studies were discussed in the context of the ECA Conference Solid Dosage Forms. In the part on equipment sourcing, for example, Dr Barthold Piening, head of global operations at Takeda and Dr Sanjit Singh Lamba, head of global procurement at Eisei Pharma, covered the differences in the purchasing of equipment for markets such as Europe and India. They agreed with regard to the statement that the cost for the acquisition of machinery and equipment is important for investment decisions, but is (not any more) the crucial criterion in most cases. Much more important are now (own and others') experiences with the potential suppliers as well as TOC (total cost of ownership) considerations, which are ultimately reflected in the production costs of the final dosage form. While Takeda mainly achieves this with less than 20 European suppliers, Eisei approaches this more differentiated. As for critical operations, mainly established European suppliers are chosen, for less critical tasks often local Asian suppliers are selected.Barrier technology - more contamination safety
In several conferences case studies on current technological issues in the production of sterile pharmaceutical products were presented.
In general, there is a trend to more contamination safety. Authorities expect the use of barrier systems and consider classic clean rooms more and more critical. Within the barrier systems the decision must be made between the classic Isolator and the RABS (restricted access barrier system). Both systems have pros and cons, and in particular the US FDA prefers the Isolator due to its increased contamination safety. In contrast to the RABS, the authority considers it to be an advanced aseptic technology.
In line with this trend Tobias Schlögl from Boehringer Ingelheim presented the upgrade of a conventional filling line on RABS with a recent case study. This three-phase project was carried out in the period from January 2013 to January 2014:
I. O ptimization of connections in product leading equipment
II. Switching the stopper transfer to DPTE technology (double door transfer port) and implementation of intervention gloves
III. Extension of the RABS-housing and integration of a vial unloading.
In particular the implementation of intervention gloves required an adaptation of the operation procedure:
- Revision of the procedures and intensive training of staff (unpacking and installation process in the clean room / pre-and post-processing of gloves / tracking of autoclave cycles in the logbook / approach when detecting defective gloves)
- Changes in the microbiological monitoring (no personnel monitoring after intervention / additional monitoring of the gloves after end of production / adaptation of monitoring plans)
- Changes / adjustments of the intervention lists
Due to the project it was possible to reduce the risk of contamination of the solution supply, the stopper transfer, in the sampling pattern and in the filling process.
Two case studies covered experiences with Isolators. While F. Hoffmann-La Roche's new parenterals operation in Kaiseraugst near Basel uses both Isolators as well as RABS, GSK Vaccines defined the Isolator as the leading technology: "GSK Vaccines has chosen Isolator technology as first choice for all future projects, if the technology is suitable for the process".
Patrick Vanhecke from GSK Vaccines summed up 15 years of experience with Isolators:
- A mock-up study is mandatory to design an Isolator successfully compliant with ergonomics and with the manufacturing process and interfaces
- An efficient partnership between supplier and customer is a key factor for a project success
- Handling of Isolator technology and related equipment requires a high level of technical expertise and a good process understanding
- Operators must be trained and certified as those working in classical aseptic area
- Isolator technology has demonstrated higher SAL (sterility assurance level) through EM and MF data
- Preventative maintenance is key for optimal use and line availability.
Roche's Isolator experience comes from the still very young parenteral facility. According to these experiences, presented by Dr Alexander Sterchi, vaporised hydrogen peroxide as a strong oxidizer can have a negative impact on the material as well as on the product. Also, accessibility within the Isolator is limited. Thus certain interventions for solving technical problems are impossible without opening the Isolator. Further, according Dr Sterchi there are limitations for material transfer via lockers. Due to format and batch changes the company sees capacity constraints on the line. For that reason large batches and campaign production are preferred. ultimately the highest contamination safety is the decisive argument for the Isolator, Dr Sterchi concluded.
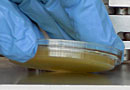
Recommendation
Barcelona, Spain4-7 November 2025
Contamination Control Strategies & Workshop Risk Assessment in Contamination Control
The suitability of Isolators for small batches with frequent batch changes was also in the centre of another case study presented by Dr Friedrich Haefele from Boehringer Ingelheim. Are Isolators really only a solution for large filling batches? or can they possibly also be used for smaller batches with frequent batch changes? In particular the change over time between 2 batches / campaigns (cleaning time / glove tests / decontamination) with specified approx. 15 hours hardly allows to operate Isolators for small batches economically. For that reason Boehringer Ingelheim in collaboration with Bausch + Ströbel and SKAN develops and implements a "flexible Isolator" in a project that has been running since 2013 and that is planned to last until 2015. Specifically developed L-flanges allow the docking of different filling systems (syringes, cartridges, vials) to a "standard Isolator" just as much as specifically designed "mouse holes" allow the docking of a quick airlock to the "standard Isolator". This concept, Dr Haefele concluded, will significantly reduce the change over time between two batches and will thus also allow an economical use for the filling of smaller batch sizes.
Author:
Dr Robert Eicher & Dr Andreas Mangel
CONCEPT HEIDELBERG