Do you know the ECA Visual Inspection Good Practice Guide?
The Visual Inspection Group was founded in 2013 as a working group of the ECA. One of the first tasks the group took up was the development of a guidance document, how the visual 100% inspection of parenterals could be carried out in a GMP-compliant way by giving concrete advice. Before that the only explicit information could be found in monograph <790> of the USP, the US American Pharmacopeia.
In the meanwhile, with chapter 5.17.2, also the European Pharmacopeia has become more detailed with respect to visual inspection. The ECA document has to be seen complementary to the concerned monographs. Modifications from the proposed procedures and figures are possible at any time. However following the proposals may lead to a safer inspection process and may avoid discussions in GMP audits. The ECA guide covers both, manual and automated visual inspection and has the following structure:
1. Manual Inspection
The section on manual visual inspection addresses the workplace and the personal carrying out the inspection. Technical details for the workplace are proposed like the very important illumination which should have at least 2.000 ux or 10.000 lux for Blow-Fill- Seal Products. The illumination should be qualified and routinely checked during preventive maintenance in intervals.Also the personnel performing the manual inspection should be qualified and re-qualified in periodic intervals. The training should be done by using training kits containing all defects relevant for the products which are inspected and under supervision of an experienced operator. The training kit only contains containers with defect. For the qualification a special qualification kit should be used focused on critical and major defects which contains about 70-80 % of "good" objects without defects. Very important for the quality of the manual inspection process are the "eye breaks" in which the inspectors rest. As a good practice 20 minutes of inspection followed by a break of at least 5 minutes for a total maximum duration not longer than 4 hours is proposed.
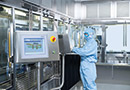
Recommendation
Cologne, Germany21-23 October 2025
Lyophilization 2025 - Includes Workshop at GEA
2. Automated Inspection
A central topic of this chapter is the qualification & validation of the automated inspection system. It has to be shown, that the automated system is at least as good as the human inspector (without magnification). The performance qualification can be rated as validation if it is carried out product specific. The ECA guide proposes to repeat the automated inspection process at least 10 times and to compare the detection rates with the results of qualified manual inspection.
Requalification should be carried out annually or every two years, as well as a revalidation should be done every 3-5 years as the automated system has to be rated as a critical system. The ECA paper proposed two different revalidation approaches. One by manual reinspection of e.g. 5000 vials of an automatically inspected batch or by a continuous revalidation approach by using AQL results.
For routine inspection the actual performance of the system should be shown before and after the inspection process by using a special function test kit.
3. Defect Classes
Following the ECA guide at least two product-specific defect classes should be defined, including critical and major defects. A third class for minor defects is recommended. Moreover the paper recommends not to include further, pure cosmetic defects for products for culturally sensitive markets into the GMP defect classification.
4. Evaluation and Trending
The results of manual and automated inspection processes should be trended. There should be limits for individual defects representative for the process capability of the inspection process. For manual inspection the ECA guide proposes 0.5/1%* for critical defects, 1-3% for major defects and 3-5% for minor defect (* there are critical defects like turbidity with an acceptance limit of 0). Typical action limits can also be set on specific defects (e.g. particles) instead of using the three categories mentioned above.
Measures to be taken for batches exceeding these limits have to be predefined. The re-inspection of a batch due a limit violation should be investigated. If a re-inspection is performed the method used for re-inspection must not necessarily be the same method used for the previous inspection.
Re-inspection should never be performed without a previous investigation why limits have been exceeded. Re-inspection should be performed independent of the initial technique used - manual, semi-automatic or automatic visual inspection, but should be limited to not more than two re-inspections.
For fully automated inspection the ECA guide recommends to define a "grey" channel eject channel for containers for which the inspection result is not clear, for example in case of machine stops or air bubbles in the product.
Re-inspection of rejected containers is not recommended and must not be performed without justification based on a thorough investigation. Re-inspection of objects in the grey channel should only be done one time.
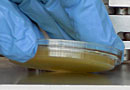
Recommendation
Barcelona, Spain4-7 November 2025
Contamination Control Strategies & Workshop Risk Assessment in Contamination Control
5. Batch Release
According to the ECA Best Practice Guide two criteria concerning visual inspection should be evaluation for the release decision: the trending analysis of the 100% batch inspection (see above) and the result of the AQL inspection. For the AQL manual inspection a randomized sampling of the 100% inspected batch should be performed according to a pre-determined AQL procedure. The document gives three limits for the three defect classes: 0 defects within the AQL samples for critical defects, AQL ? 0.65 for major defects and ? 4.0 for minor defects. If an AQL limit is exceeded, the whole batch may be re-inspected 100% followed by a second AQL manual inspection. This process can be repeated, but must be justified by an investigation and should not be performed more than 2 times in maximum. The paper moreover recommends using the AQL approach in case of particles found in batches already released to the market. The relative batch and sample size will determine the acceptance criteria of the AQL test. If these criteria are met, the batch can be considered essentially free of particles Download of the Good Practice Guide is possible for free. After a registration on the website of the ECA Visual Inspection Group www.visual-inspection.org access to the member's area is granted where - amongst other helpful information - the recent version 3.2 of the paper can be found.
Author:
Dr Robert Eicher
...is Operations Director and organises and conducts courses and conferences on behalf of the ECA Academy around pharma technology.