Conference Report on the ECA Equipment Qualification Forum
Following last year's release of version 2.2 of the ECA Good Practice Guide "Qualification and Validation - A guide to effective qualification based on Customer - Supplier Partnership", the new version 3.0 has now been published. It was presented for the first time at the Equipment Qualification Forum.
Authors and users of the guide explained its content and practical applications to more than 40 participants from 13 different countries who attended the forum. At the beginning of the event, Ralf Gegenbach, current Chair of the ECA Validation Group, provided an overview of the current guide and highlighted the changes from last year's version 2.2. Inspector feedback was incorporated and the chapters on CARA (Critical Aspects Risk Assessment), categorisation, and remote testing were revised.
The aim of the guide is to outline practical solutions, to include case studies, and to provide sample templates for "lean qualification". The guide links the requirements from Annex 15 of the EU GMP Guide to the FDA Process Validation Guidance and the ASTM Standard E2500 approach (see Figure 1 on page 20).
Through a strict and risk-based approach, the ECA Guide outlines how to integrate suppliers into the qualification process. It is therefore well aligned with the ISPE Guide "Commissioning and Qualification," 2nd Edition (2019). While ISPE emphasises the process flow, the ECA Guide focuses on the roles and responsibilities of the different parties involved in equipment qualification (see Figure 2 on page 20).
This was followed by a presentation from Klaus Eichmüller, a European GMP Inspector who actively participated in the revision of Annex 15. He began by providing an overview of the regulatory landscape related to qualification and validation. Although the revision of Annex 15 dates back almost ten years, he emphasised the significance of the changes, noting that even nearly a decade later, many companies have yet to implement all the updated requirements.
He addressed the expectations for suppliers involved in qualification activities. A contractual agreement between client and contractor is mandatory. The client remains responsible and must supervise and approve the contractor's work. He also pointed out that categorisation of equipment is possible - a topic revisited by Maik Guttzeit on day 2.

Recommendation
30 September / 1 October 2025
Process Validation - Live Online Training
He concluded by presenting a slide which summarised typical deficiencies he observed in qualification processes (see Figure 3).
Figure 1: ECA Guide Focus - Supplier's involvement
Figure 2: ECA vs ISPE Guide
Figure 3: Qualification - problems
Ralf Gengenbach returned to address the topic of comparing regulatory guidelines. He highlighted key differences between the various approaches:
- Subject Matter Expert vs. QA (ASTM/ISPE vs. Annex 15)
- QCU vs. Head of Production (FDA Process Validation Guidance vs. EU GMP Guide I)
- Is the traditional V-model still valid - and if so, how should risk management be integrated?
He also noted that the terms such as DQ, IQ, OQ, and PQ are referenced inconsistently or even omitted in some guidelines. Nevertheless, he sees no substantial differences in qualification practices across the various standards.
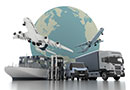
Recommendation
Thursday, 9 October 2025 9 .00 - 12.30 h
Temperature-sensitive Pharmaceuticals – Transport and Vehicle Qualification - Live Online Training
The updates to the chapter on "Critical Aspects Risk Assessment" (CARA) were presented by Rafael Leandro de Souza from Pharmaplan. He began by emphasising that equipment qualification is a lifecycle process that should be documented to ensure traceability. He then demonstrated how the CARA concept can be integrated into the qualification lifecycle (see Figure 4 on page 21).
Figure 4: The CARA concept in the equipment qualification life cycle
The first quality risk assessment, referred to as QRA 0, identifies product-related risks (CQA), product-equipment-related risks (CPP), and process and production environment-related risks (CTQ). These parameters feed into the equipment design. The second risk assessment, QRA1, evaluates the QRA0 parameters against GMP requirements. These evaluations inform the User Requirements Specification (URS), which, following the CARA model, is also structured in three stages.
QRA2, performed during Design Qualification, assesses the equipment design during the design reviews. In QRA3, the testing strategy and a GMP traceability matrix are defined. QRA3 also covers both the commissioning (GEP) and qualification (GMP) phases, resulting in a GEP-based testing strategy and GEP traceability matrix. Finally, he illustrated how the process elements of ICH Q9 Quality Risk Management can be mapped to CARA 0-3 risk assessments (see Figure 5).
Figure 5: CARA and QRM
A presentation by Dr Clemens Borkenstein (ZETA GmbH) and Rolf Bauer (Syntegon Technology GmbH) on remote testing during Factory and Site Acceptance Tests (FAT/SAT) was intensely discussed. Dr Borkenstein, head of the ECA Validation Group's Remote Testing Subgroup, and Mr Bauer, a subgroup member, noted that the ECA Guide was the first to formally address remote testing in equipment qualification.
They presented a comprehensive checklist outlining what to consider before, during, and after remote testing. A new section on "Remote and Hybrid Testing" was added to the updated chapter. These are tests where one party observes remotely via computer, while personnel are present on-site to conduct and support the tests directly. Practical examples - including video demonstrations - illustrated how remote testing is conducted at ZETA and Syntegon.
The presentation concluded with a discussion of the advantages and di advantages of remote testing (see Figures 6 on this page and 7 on page 22).
Figure 6: Pros (for live stream FAT)
Figure 7: Cons (for live stream FAT)
This concluded the first day of the conference.
Day two began with a presentation by Maik Guttzeit from Bayer AG. He leads the subgroup on prioritisation within the ECA Validation Group. Using two examples - a balance and a freeze-dryer - he highlighted the challenges that seemingly simple equipment can pose during categorisation. His initial conclusion was clear: there are no easy or clear-cut answers when it comes to categorisation.
He went on to present a three-tiered categorisation model, dividing equipment into:
- Non-critical
- Low-critical
- Critical
He substantiated these categories with examples, particularly in relation to qualification activities. For commercial off-the-shelf (COTS) equipment, Maik Guttzeit illustrated opportunities for simplification with respect to Design Qualification (DQ) and Installation Qualification (IQ).
He then presented the current status of Annex 9 of the ECA Good Practice Guide, which specifically addresses categorisation. According to Maik Guttzeit, various categorisation approaches are possible:
- A matrix-based approach with a traffic light system: red, yellow, green (see Figure 8)
- A decision tree model
- A tabular approach
Figure 8: Categorisation – Matrix Approach
His closing message was: Categorisation can help reduce the qualification effort - but it should never compromise quality.
The topic of electronic documentation within qualification projects was addressed by Igor Krasula of Valicare and Dr Clemens Borkenstein, each providing practical case studies. The benefits of electronic documentation were outlined, including:
- Improved legibility of reports and easier translation, if required
- Enhanced data integrity
- Easier document sharing (e.g. for approval processes)
- Faster documentation and more consistent terminology (through the use of standard terms)
- Electronic approvals (e.g. via digital signatures)
- Direct integration of test data (from the equipment itself, cameras, control panel printouts, etc.)
- Easier and more cost-effective archiving
He contrasted the "traditional approach" (scanning paper-based documentation) with a more "advanced approach", where qualification/validation documentation is created electronically, tests are entered directly into the system, and the documentation is reviewed and approved electronically (see Figure 9).
Figure 9: Advanced Approach
It was important to him to emphasise that electronic systems comply with data integrity principles such as ALCOA+ and ALCOA++. He cited PIC/S PI 041 as a valuable resource. When planning an electronic documentation system, particular attention should be paid to the interfaces between supplier and customer, the associated workflows, and the system architecture itself.
When planning an electronic documentation system, particular attention should be paid to the interfaces between supplier and customer, the associated workflows, and the system architecture itself.
In conclusion, Igor Krasula noted that while some companies are still at the beginning of implementing electronic systems, others have already made significant progress. Regardless, the field is clearly moving away from "tons of paper" towards fully electronic documentation. The highlight of the session was a live demonstration of such a system. It powerfully illustrated how appropriate field programming can prevent errors by guiding users through predefined data entry worflows.
In the penultimate presentation, Pia Loris from Drees & Sommer addressed project management in qualification projects. She identified the main challenges in such projects according to six factors:
- Process complexity (e.g. integration of diverse systems and processes can be intricate)
- Lack of resources (e.g. unsuitable suppliers or insufficiently experienced personnel can delay progress)
- Regulatory compliance (e.g. keeping up with evolving requirements and audit readiness can prove demanding)
- Technological challenges (e.g. validating complex software systems and ensuring reliable equipment operation)
- Risk management (a critical element in qualification, but often time-consuming and difficult due to the absence of contingency buffers)
- Data integrity (handling large data volumes while ensuring their integrity can also present a major challenge)
Using an overview diagram, she illustrated the complexity of Good Engineering Practice (GEP) activities versus qualification activities (see Figure 10).
Figure 10: Good Engineering Phases vs Qualification Phases
The final speaker was Dominik Unglaub from gempex, speaking from their Swiss site, who shared his first-hand experiences from audits and regulatory inspections relating to equipment qualification.
He opened his talk with the rhetorical question: How deeply do inspectors delve into equipment qualification? He answered this through two case studies - one involving two days of inspection, the other four days. In both cases, the primary focus was on user requirements and the associated documentation.
He shared several inspection findings, including:
- Lack of Standard Operating Procedures (SOPs) for operation, cleaning, and maintenance, despite Performance Qualification (PQ) testing already having been conducted.
- Absence of binding timelines for resolving qualification deficiencies.
- The validation master plan did not ensure that all deficiencies impacting qualification were appropriately addressed.
His conclusion: The User Requirement Specification (URS) is the key document in equipment qualification. Traceability within documentation is essential. Inspection depth has increased significantly in recent years, a sentiment that was echoed by attendees in the audience.
As part of a workshop, the application of Artificial Intelligence (AI) in qualification was demonstrated, using ChatGPT as an example.
The AI was tasked with summarising a subchapter from the Good Practice Guide on the supplier-customer relationship - and completed the task impressively.
On a spontaneous prompt from the audience, ChatGPT even generated a song with the fitting title "Keep it Confidential". A separate AI tool later composed accompanying music, and the full version of the song is now available on the Validation Group website: www.validation-group.org.
Title: "Keep It Confidential"
(From ECA IG Validation Guide 3.0)
(Verse 1)
We've got secrets, kept under lock and key, Product and process, only for us to see.
In a document called PPURS, Where every step and risk is laid out first.
(Chorus)
Keep it confidential, keep it safe and sound, With every single process, as we go around.
We'll find the right supplier, with care and review, Then set the plan together, me and you.
(Verse 2)
We gather round, in a workshop or two, Discussing details, making them true.
The final requirements, agreed side-by-side, So every single step, we know and guide.
(Chorus)
Keep it confidential, keep it safe and sound, With every single process, as we go around.
We'll find the right supplier, with care and review, Then set the plan together, me and you.
(Bridge)
And if we share a little secret, We've got that NDA, So what's important stays protected, Every step of the way.
(Chorus) Keep it confidential, keep it safe and sound, With every single process, as we go around.
We'll find the right supplier, with care and review, Then set the plan together, me and you.
(Outro) From PPURS to the URS, We're setting it all up for the best success.
Keep it confidential, keep it safe and true, Together on this journey, me and you.
Though AI successfully completed its first task, there were also limitations. When tasked with a ppm calculation, ChatGPT completely failed.
The takeaway here: Using AI in equipment qualification can be genuinely helpful - for instance, in generating reports - but the results should always be critically assessed.
A final summary of the event as a whole: the presentation of version 3.0 of the ECA Good Practice Guide Qualification and Validation demonstrated the value of an in-person event. The social gathering in Heidelberg's old town offered opportunities for exchange that would not have been possible in an online format.
One suggestion for improvement was to make the Guide available in a simplified edition, aimed at (still) less experienced suppliers operating within the GMP environment. The ECA Validation Group will be working on this over the course of the year.
The Guide is available free of charge to members of the Validation Group - see www.validation-group.org. |
About the Author
Sven Pommeranz is Operations Director and organises and conducts courses and conferences on behalf of the ECA Academy in the area validation.