Cold WFI Manufacture - Two Years after the Change in the Pharmacopoeia
In April 2017 a significant change in the European Pharmacopoeia became effective: After - incl. predecessors - almost 100 years, the regulation for the production of water for injection (WFI) was changed, the requirement "distillation" was deleted.
The new requirement of monograph 169 on WFI production is
Water for injections in bulk is ... produced either by:
- distillation in an apparatus of which the parts in contact with the water are of neutral glass, quartz or a suitable metal and which is fitted with an effective device to prevent the entrainment of droplets;
- a purification process that is equivalent to distillation. Reverse osmosis, which may be single-pass or double-pass, coupled with other appropriate techniques such as electro-deionisation, ultrafiltration or nanofiltration, is suitable. Notice is given to the supervisory authority of the manufacturer before implementation.1
This change was preceded by years of discussions. The US and also the Japanese pharmacopoeia had already refrained from the requirement of distillation for a long time. Engineering technology had already considered evaporation and condensation an inefficient purification method for the manufacture of WFI since the early 1990s. In particular the advances in membrane technology (reverse osmosis, electro-deionisation, ultrafiltration) had clearly shown, for example in the electronics industry, that ultrapure water of the highest microbiological quality can be produced without the phase transition of distillation.
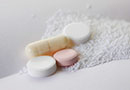
Recommendation
14-16 October 2025
Granulation & Tableting - Live Online Training
However, there was little interest from the regulatory authorities in Europe to allow membrane processes as an alternative to distillation. In 2002, this resulted in a special solution: the quality Highly Purified Water (HPW) was introduced in the European Pharmacopoeia2. The specification of all relevant release values (conductivity, TOC, endotoxins, germs) was the same for HPW and WFI - only that distillation was still specified as the production method for WFI from 2002 to 2017. During this period, the HPW systems showed that no "steam machine" is needed to manufacture water that meets the specification for WFI. The use of HPW made sense for large sterile operations, which could now operate their vial / syringe / ampoule washing systems with HPW instead of WFI at considerably lower costs.
Today, the costs for the different water qualities in pharmaceutical manufacture are as follows:
- Drinking water approx. 1 - 12 € / m³
- Purified Water / Highly Purified Water approx. 10 - 25 € / m³
- WFI cold with membrane process approx. (should be the same as HPW and clearly less than WFI - reliable figures are not yet available)
- WFI hot with distillery approx. 50 - 100 € / m³
- WFI in pharmacy: 1.000 - 20.000 € / m³
In this respect, HPW quality has helped pave the way for the amendment of the European Pharmacopoeia in 2017. It was expected that the costs for cold WFI with membrane processes would be about the same as for HPW.
Until today the proponents of distillation technology argue as follows: If the USA and Japan have not been requiring distillation for such a long time, why is it that WFI is still manufactured worldwide mainly by distillation?
There are major reasons for that, though:
1) As long as distillation was mandatory in Europe, every company selling globally had to comply with the requirements in Europe.
2) To manufacture WFI safely with membrane technology, one needs a very good, stable, high-quality drinking water supply. This is available in 50% of Europe, but not in many areas in the rest of the world.
3) In other regions of growing importance, such as China, distillation is still the only permitted production method for WFI.
In Europe, a Questions & Answers paper for European GMP inspectors became effective in 2017, which does not reflect the current state of the art3. This is also the opinion of the PDA, which approached the EMA in November 2016 with a letter4. For instance, the following statement can be found in the EMA Q&A paper:
"The RO5 membranes are currently not designed to withstand pressurised steam, but those that are capable of withstanding high temperatures are available and should be utilised in order to allow for routine high temperature flush through the system in conjunction with routine chemical sanitisation."
The steaming (121 °C) of RO membranes does not appear to be sensible, since the known water germs are also killed at lower temperatures such as 80 °C. The phase transition steam-water would damage the only 0.2 μm thick jelly diffusion layer of the membrane due to the large volume change. It is also not possible to sanitize an RO in a meaningful chemical way. The chemicals cannot pass through the RO membrane, and RO wrap modules cannot be backwashed. No HPW plant has ever been built and operated this way.
Extremely critical, however, is another demand that can at least not easily be rejected.
It is undisputed that a distillery - after the vapour-liquid phase transition - always produces WFI without viable germs according to the agar plate colony count test method. However, a breakthrough of such germs can occur in cold WFI manufacture using membrane technology. Therefore the EMA-Q&A-Paper demands:
"Use of rapid microbiological methods should be considered as part of the control strategy to aid with rapid responses to deterioration of the system." und "Quantitative microbiological test methods - in line with Ph.Eur. 5.1.6 monograph 'Alternative Methods for control of Microbiological Quality'."
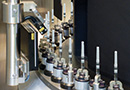
Recommendation
Vienna, Austria21-23 October 2025
Visual Inspection of Parenterals PLUS Pre-Course Fundamentals of Visual Inspection
It is undisputed that counting germs by the plate method is not the most modern method. There are the "alternative methods" for microbial count. However, it is the case that all these alternative methods find considerably higher bacterial counts. A successful validation - especially the assurance of comparability - has therefore not been successful so far6.
As of today, the batch release for medicinal products manufactured with WFI is therefore still carried out using the agar plate method.
Nevertheless, some companies have started planning and installing WFI generators with membrane technology. Many assume that the specifications of the EMA Q&A paper will be technically revised - and even though considering the document for that reason, deliberately do not implement some of the required measures. However, many companies do not want to take any compliance risk. For this reason, new WFI producers continue to opt for the old "steam machine technology".
With the EMA Q&A paper we have, in the author's opinion, a case of outdated regulation which hinders progress and leads to avoidable additional costs in the manufacture of medicinal products. An important locational advantage of Central and Northern Europeans - the availability of very good feed water as an excellent prerequisite for the use of the cold WFI manufacturing processes - is thereby eliminated. Whether and when these obstacles can be eliminated, and how fast the WFI manufacture with membrane processes will prevail, cannot be predicted today.
Author:
Markus Multhauf
... is a senior engineer and has been working as a freelance engineer in the field of GMP pharmaceutical technology since 2013.
Source:
1 European Pharmacopoeia , www.edqm.eu; Monograph Water for Injections 2017-2019
2 Note for Guidance on Quality of water for pharmaceutical use (2002)
3 www.ema.europa.eu/documents/other/questions-answers-production-water-injections-non-distillation-methods-reverse-osmosis-biofilms_en.pdf (link re-checked Jul. 2019)
4 www.pda.org/docs/default-source/website-document-library/scientific-and-regulatory-affairs/regulatory-comments-resources/2016/ema-qa-production-of-wfi-by-non-distillationmethods-submitted-4-nov-2016.pdf?sfvrsn=4 (link re-checked Dec. 2018)
5 RO = Reverse Osmosis
6 See presentation Pharma-Lounge 5.-7.Feb.2019 R.Roepenack, Robert Bosch Packaging Technology GmbH; Membrane based WFI manufacture according to revised monograph 0169 Ph.Eur. + K.-P.Mang, Mettler-Toledo GmbH; Experience with new technologies for determining bacterial count in pharmaceutical water in real time + R.Scheibel, PMT Partikel-Messtechnik GmbH; Possibilities for continuous microbial process control + A.Minzenmay, BWT Pharma & Biotech GmbH; Driniking water to WFI (Ph.Eur.) with a membrane device + U.Träger, Wilhelm Werner GmbH; Cold WFI manufacture - project introduction + T.Rücker, Letzner Wasseraufbereitung GmbH; Biofilm control strategies in pharma water treatment + P.Kreutzenbeck, Roche Diagnostics GmbH; Trend microbiology On-line - Rapid Microbiological Method