Cleaning Validation Q&A
In September 2020, the ECA offered the first Cleaning Validation Online Training Course. Many questions were asked to the speaker. Below you will find a number of questions which have been answered by Robert Schwarz from the FH Campus in Vienna.
Selection of Q&As during Live Online Training Cleaning Validation. All answers reflect the opinion of the speaker based on his experience.
1. Question: Regarding visual inspection of surfaces in Annex 15: Is during operator qualification a training on the relevant SOP sufficient or should a training, comparable to those for visual inspection operators, be established (incl. periodic eye sight test)?
Answer: A solely theoretical SOP-training is not sufficient. Practical training with surface samples spiked with different concentration of the respective product needs to be performed. This needs to be performed by collecting data to demonstrate down to which level of residues visual cleanliness can be detected.
2. Question: Are direct sampling methods necessary for transfer lines or other inaccessible equipment parts? Those parts can neither be tested visually nor via swab testing. Would final rinse testing be sufficient?
Answer: This clearly depends on factors like pipe length, flow conditions, percentage of surface area that can't be inspected and should be addressed in a risk assessment. Additional measurements like endoscopic inspection as part of maintenance could also be beneficial. Taking the solubility of residues into consideration final rinse sampling could be sufficient.
3. Question: Are PDE values applicable in products that are only applied once or twice (e.g. vaccines)?
Answer: Yes, PDE values derived from HBEL are also applicable. They need to be established for every medicinal product. Only if inactivation during the cleaning process could be shown a risk based strategy could be developed where applying the PDE is not needed:
"In view of this, the determination of health-based exposure limits using PDE limits of the active and intact product may not be required."
4. Question: If you introduce a new product in a multi-purpose facility and identify this product as worst case; do you have to revalidate the cleaning process for existing equipment?
Answer: Yes, a revalidation is necessary. The extent needs to be defined in a risk assessment.

Recommendation
30 September / 1 October 2025
Process Validation - Live Online Training
5. Question: Is there a reason why a CHT and Sterile Hold Time (SHT) could not be shown within one single validation protocol? In the way that sampling will just be done at the end of SHT?
Answer: Yes, testing for CHT is first performed before sterilization having data within the accepted limit for bioburden (rinsing, swabbing or contact plate sampling) prior sterilization. This also is the minimum bioburden to inactivate via sterilization (excl. buffer -> SAL) - basis for sterilization validation.
SHT has nothing to do with cleaning validation. It is linked to sterilization validation, aseptic processing and aseptic process simulation (media fill). Validity can either be shown via sampling or can be covered, based on a profound risk assessment, in an aseptic process simulation.
If you sample only after SHT you have no data for bioburden prior sterilization and therefore no data for CHT.
The only scenario I could imagine to skip CHT is a CIP/SIP process where sterilization is automatically directly started after the cleaning process. Therefore there is no CHT, so only SHT needs to be validated. But at least you need data for endotoxins after cleaning.
6. Question: What about sampling of wire-mesh filters of fabrics filters?
Answer: According to my experience sampling wire mesh filters of fabrics filters is only possible via rinse sampling.
7. Question: Can the worst-case substance regarding to cleaning also be determined by only performing theoretical calculations and w/o performing any practical small scale studies in the lab?
Answer: Based on my experience with several research projects predicting cleanability of a product or component solely based on theoretical data like physico-chemical parameters and model assumptions are insufficient and lead to a "trial &error"-like cleaning validation.
8. Question: For the manufacturing of solid oral forms: Our local authorities still insist that we need to re-introduce the 10ppm criteria even though PDE-values are available for all products produced in our facility. What could be the intention of this requirement?
Answer: Based on the information the only rational behind this request would be that the authority usually complains in this case, and which was also addressed in question 6 on Q&A on the "shared" facilities guideline, is the replacement of existing limits (e.g. 10ppm) by PDE-based limits, especially if these are higher:
"For existing products, manufacturer's historically used cleaning limits that should be retained and can be considered as alert limits, provided that when taking cleaning process capability into account, they provide sufficient assurance that excursions above the HBEL will be prevented. A similar process should be adopted when establishing cleaning alert levels for products introduced into a facility for the first-time."
9. Question: If e.g. one out of several swabs is OOS, is it possible to calculate the real carry-over from the achieved swab values and compare it to the MACO? So that not all relative (to surface) values need to be in spec but the final absolute carry-over value
Answer: No, on of the fundamental assumption that swab sampling could be performed is that the residues are evenly distributed on the surface. Additionally regulators generally see it critical if some sort of mean value calculation is performed (compare microbiological environmental monitoring according Annex 1).
10. Question: What to do first, swab or rinse, if you are doing both?
Answer: I would recommend to perform final rinse before swab sampling so no interference from swab sampling could affect the rinse sample.
11. Question: Which microbiologic method do you consider more representative/complete: rinsing, plates or swabbing?
Answer: Based on my experience recovery rates of rinse and contact plate sampling are often higher than those for swabbing. Some colleagues even call microbiological swabs a "qualitative" sampling. For sampling curved surface areas I even would recommend flexible contact plates over swabbing.
12. Question: For determination of cleaning agent residue: would a conductivity meas-urement in the final rinse be totally enough for a cleaning validation or should a direct sampling via Swab and TOC analytics be added at least to verify the results from conductivity?
Answer: If the composition of the cleaning media is a simple anorganic acid or base the concentration of it in the media and also final rinse sample has a high correlation factor to conductivity measurement. This is also one reason why especially for Biologics and Biotech products NaOH is frequently used.
13. Question: What are the regulatory requirements for recovery for swab tests during method validation, is there a percental limit?
Answer: There are no explicit regulatory requirements regarding chemical swab recovery rate. Common practice is e.g. reflected in PDAs TR No. 29; Section 6.5.2 "Swab/Wipe recovery":
"An acceptable swab recovery depends on how that swab recovery is being used. If the recovery is performed to qualify the sampling method without correction of either a limit or an analytical result then a recovery percentage such as 70% or more is typically required. If the recovery percentage is used to correct a residue limit or an analytical result then a recovery of 50% or more is typically required. An upper limit for percent recovery should be established to deal with studies where the measured recovery is greater than 100%. Recoveries of less than 50% typically require a written rationale of why that percentage is appropriate."
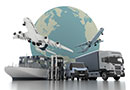
Recommendation
Thursday, 9 October 2025 9 .00 - 12.30 h
Temperature-sensitive Pharmaceuticals – Transport and Vehicle Qualification - Live Online Training
14. Question: Is it acceptable after CHT is exceeded to carry out only a disinfection of the equipment or is it obligatory to repeat the whole cleaning process?
Answer: Generally CHT has nothing to do with disinfection. Also, it is not advisable to disinfect product contact surfaces with potential risk of leaving disinfecting agent residues on the surface. It should be assessed on a risk-based approach if only final rinsing is sufficient or the whole cleaning process needs to be repeated.
Author:
Robert Schwarz
... is a university lecturer at FH Campus Vienna, Austria. He has 20 years hands-on experience in aseptic processing, contamination control and cleanroom technology.