CAPA AS A CENTRAL SYSTEM FOR IMPROVEMENT PROCESSES
In the pharmaceutical industry, it is becoming more and more important to carry out corrective and preventive action after the recovery of failures and deviations. Due to the implementation of CAPA (Corrective and Preventive Action) in guidelines such as ICH Q10 and FDA's Quality System Guide, the expectations of the supervisory authorities regarding such systems also increase. The systems should be shaped and used efficiently - not only because of these expectations, but especially since the CAPA system is the central system of continuous improvement processes in the GMP sector.
The CAPA process can be divided into several process steps:
1. Detecting and understanding failures1
The creation of positive failure awareness is essential for a successful CAPA system. Employees as well as superiors have to accept that people make mistakes. These should not be considered a flaw but be understood as an opportunity. Otherwise there is the danger of correcting failures immediately or of concealing or downplaying them. But all failures have to be addressed and registered immediately. Other sources of information are complaints, trend analyses and observations within audits and inspections.
2. Investigation of the root cause
The right measures can only be deduced and decided when the real root cause has been determined. Simply training the alleged perpetrator will not have the desired success. And this leads to negative failure awareness.
3. Determination, implementation and verification of necessary measures
The necessary measures have to be deduced causally from the root cause and they must be formulated precisely. A risk analysis might help in the case of any necessary prioritisation. Persons in charge have to be appointed for the activities identified and realistic timeframes determined. Performance has to be monitored and assessed with regard to efficiency.
4. Conclusion
All measures and action plans have to be concluded formally and the parties involved informed about the results.
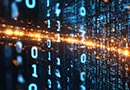
Recommendation
Copenhagen, Denmark26 August 2025
Raw Data - Understanding, Defining and Managing
Implementation of a CAPA System
Often a CAPA system has to be integrated into a quality management system in addition to prevailing systems such as deviation management, complaint handling, OOS procedure, change control and implementation of observations within audits and inspections. Two possibilities should be taken into consideration by a pharmaceutical company:1. "All-in-one" syste
The CAPA system replaces or integrates other systems completely. There are only differences at registration level. The advantages of such a comprehensive system are obvious: all failures are registered and processed in one system. Furthermore connections are recognisable more easily, cross-references are possible and demand analyses and resource planning are easy to survey. In general there is no danger of losing focus. Because of this increased transparency, the efficiency of the measures can be seen more easily and reporting on all activities is simplified. But the (new) implementation is resource-intensive. Many processes have to be adapted. Often new IT systems have to be introduced which means more training expenditure. Starting difficulties have to be expected.
2. Multiple systems
In this case, the actual systems or parts of the quality management systems persist more or less independently and only bigger processes or projects are passed on to the CAPA system. Naturally it is more difficult to see connections and often there is no overview of total activities and processes. Even if such a multiple system is allegedly the cheaper alternative, it should be taken into consideration that any possible inefficiency could cause higher costs. Several parallel systems also mean more validation, more maintenance and more constant training.
Each company must decide whether a fully electronic system should describe the CAPA process or whether a paper- based system is sufficient. The advantages and disadvantages are outlined below:
The size of the company has a crucial influence on the decision. Indeed, a paper or corresponding hybrid system might be sufficient for small companies or sites. The bigger the company and the more batches are produced and processes evaluated the greater the advantages of an ITcontrolled system. Independent of the actual form of CAPA system it is necessary to make sure that all interfaces are identified and that the requisite information can be obtained. All failures should be registered and appropriate measures taken and implemented. Only then will it be possible to learn from failure and a continuous improvement process be initiated.
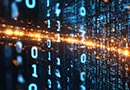
Recommendation
Copenhagen, Denmark27-29 August 2025
Data Integrity Master Class
Conclusion
What can be learned from failures? This question is similar to the one about the possibilities of learning from history. The future is and remains difficult to predict and can not always be shaped in the way one wishes. But it is possible to see what has to be avoided at all costs.
Author:
Wolfgang Schmitt
CONCEPT HEIDELBERG
Source:
1 In this article failure means a result or a process that deviates from the norm. This concept includes failures during implementation and other deviations.