Air-tightness of Cleanrooms and Containment Solutions - Classification, Planning & Testing
The need for standardized definition and testing of the air-tightness of rooms is growing. Reasons for this include the increasing use of hydrogen peroxide and other volatile decontamination media, the increased use of toxic substances in the pharmaceutical industry, and the increased handling of dangerous pathogens and genetically modified organisms. Air-tightness also plays a significant role in energy efficiency requirements.
All known regulations (DIN EN ISO 9972, VDI 2083 Part 3 and DIN EN ISO 14644-3, DIN EN ISO 14644-7, ISO 10648-2, Canadian Containment Standards for Veterinary Facilities, AS/NZS 2243-3) describe different procedures for implementation and are not directly comparable in terms of acceptance criteria and measurement results. However, there is not only a lack of purely metrological standardization. If room tightness is not considered comprehensively across all project phases, the client may order an unspecified "airtight" cleanroom and discover during air-tightness testing that unacceptably large leakage air volume flows are present. Leakage detection and correction then need to be carried out in a very time-consuming and detailed process. Many faulty installations cannot be corrected retrospectively, or only at considerable expense in terms of time and money, because access is often no longer possible. This applies above all to cleanroom penetrations, i.e. openings for supply lines, cables, etc. in cleanroom walls and ceilings.
The most common weak points for air-tightness are usually:
- Ventilation network (flanges, fixtures, fittings), ventilation outlets
- Connections of machines, pipe ducts
- Doors (hinges), closing latch
- Connections/passages to neighboring rooms
- Joints in the wall and ceiling system
- Electrical installation, cable ducts
- Monitoring sensors
The biggest problems are the following:
- Interfaces of the systems (penetrations through walls and ceilings) -> Who is responsible for the system?
- No information of the individual system components (leakage
budgets) - Time-consuming search and improvement of leakages retrospectively
-> Reworking
This is remedied by VDI Guideline 2083 Sheet 19 of 08/2018. This guideline, which receives less attention in the international arena, specifies a procedure for testing and classifying the air-tightness of containments, usually cleanrooms, air ducts, but also comparable equipment and parts, and contains instructions for establishing airtight cleanrooms. The procedure can be applied correspondingly to other rooms whose air-tightness is to be verified, such as:
- Cleanrooms in general
- Cleanrooms with decontamination systems, e.g. H2O2 gassing
- Laboratories with special requirements
- Isolators
Figure 1: Example leakage detection at ducts, Source: N. Ferstl
The application to similar areas (e.g. adjacent controlled areas) with special requirements is possible and sensible. The guideline applies to all spaces that require positive or negative pressure compared to the environment during operation in order to meet a certain protection goal (product protection, personal protection, ambient protection, environmental protection). The air-tightness requirements are based on the hazards that may be caused by leakages. The scope of the testing, the performance of the it and, if necessary, the leakage detection are in turn dependent on the air-tightness requirements.
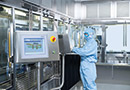
Recommendation
Cologne, Germany21-23 October 2025
Lyophilization 2025 - Includes Workshop at GEA
In particular, the following procedure should be followed:
1) Holistic consideration of room air-tightness across all project phases.
- Selection of room air-tightness classes for the respective application based on a risk analysis (only as high as necessary).
The VDI recommendation is described in the appendix - Recommendation for the planning and execution of the cleanroom shell with clarification of the interfaces to process and building technology systems that penetrate the cleanroom,
- in particular the sequence of operations
- accessibility for assembly and maintenance
- Connections/passages that cannot be accessed later should be designed to be maintenance-free and tested during construction
- Planning and execution of the air-tightness test
2) Uniform classification for various applications in the clean environment
3) Defined and detailed measurement and test procedures
Holistic approach
The VDI guideline provides a uniform classification for a wide range of applications in clean environments, from cleanrooms to isolators to high-security laboratories.
The classification of the air-tightness of containments is based on the definitions in DIN EN 15727. The air duct tightness classes A to D according to DIN EN 15727, which have nothing to do with the EU GMP cleanroom classes A-D, are integrated into the tightness classes of containments presented in the VDI guideline and are identical to the tightness classes 1 to 4. This makes it possible to test an entire system consisting of one or more rooms and the associated air ducts and components (e.g. filter and damper casings) as a unit. The air permeability is relative to the room-enclosing surfaces of the containment. Since a certain number of ventilation ducts belong to each containment, this results in a conformity of the air-tightness requirements. Starting from the specification of the air-tightness requirement, the entire planning process is described, up to the planning of the air-tightness tests. In addition, monitoring during construction and qualification/requalification are addressed. The guideline recommends that a person responsible for the system ("authority") be appointed to take care of the overall coordination of all sealing measures. This person oversees the entire planning, implementation and qualification process until the system is released for use. The guideline also includes detailed measurement and test procedures for the entire containment, for subsystems and individual components, which serve to provide reproducible proof of air-tightness.
The air-tightness of a containment is defined by specifying an airtightness class (0-7) and a differential pressure reference. This is shown in a graphic in the VDI standard. The guideline gives the following recommendations for the air-tightness classes:
- Class 0: For ventilated rooms with lower requirements than ISO 9 or energy efficiency requirements in general (can be used in a GMP facility).
- Class 1: Cleanrooms ISO 7 to 9 or classes C and D according to EU GMP
- Class 2: Rooms that are kept under negative pressure in a controlled manner during a gassing process.
- Class 3: Cleanrooms <= ISO 6 - i.e. class B and better according to EU GMP
- Class 4: BSL3 safety laboratories; sterile isolators and rooms that are fumigated
- Class 5: Safety laboratories BSL4, active substance isolators (High Potent)
- Class 6/7: Project-specific special requirements for rooms with extremely high demands on air-tightness, e.g. high-security laboratories (usually not found in a GMP facility)
The overall relationship between tightness classes 0 to 7 and cleanroom class according to DIN EN ISO 14644 Part 1 or EU GMP Guideline Annex 1 can be seen in the figure above.
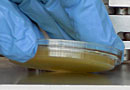
Recommendation
Barcelona, Spain4-7 November 2025
Contamination Control Strategies & Workshop Risk Assessment in Contamination Control
Summary
Air-tightness is defined by specifying an air tightness class (0-7) and a differential pressure reference. The requirements for tightness are considered to be met if the containment complies with the air permeability limit at the differential pressure reference. Based on the guideline, the air-tightness requirements can be defined and metrologically verified for all relevant containments of cleanroom technology that are operated at usual differential pressures. Thus, a practice-oriented procedure is available that describes the requirements for all relevant project phases from planning and construction to qualification.
About the Author
Nikolaus Ferstl
... is the technical director of the University Hospital and the University of Regensburg. He is also a freelance consultant for building and cleanroom technology.